New Perspectives on Freeze-Drying
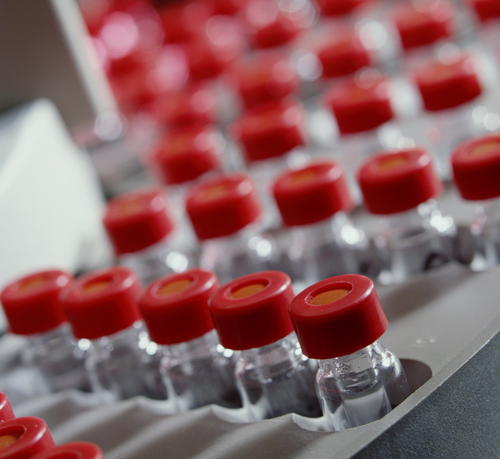
Freeze-drying technology has been constantly evolving. In terms of validation, quality-by-design (QbD) has replaced the classical approach to increasing product knowledge. With QbD, a design space can be defined in which the process can vary without impacting the critical quality attributes of the product.
The next advancement will be to develop a dynamic system, one able to give information on sublimation and product temperature evolution during the cycle, to replace the static system. In terms of validation, a commonly used strategy is one in which the heat transfer coefficient for the device and the freeze-dryer is determined. The resistance of the product is measured, and freeze-dryer capability monitored to avoid chocked flow. With those three elements, the scale-up and transfer of product is no longer empirical but can be predicted. The sensors able to monitor the cycle are also evolving. For example, a mass spectrometer can be installed on a freeze-dryer that uses wireless probes to determine potential leakage of silicone oil. This tool can also monitor the end point of primary drying.
In the past, refrigerants were improved to avoid ozone depletion, but they still have a high potential to contribute to global warming. The 2015 F-gas regulation targets cutting these emissions in the United States by two-thirds by 2030, and the first major reduction has recently come into force. In 2018, the distributor may sell only refrigerants with a CO2 equivalent to 63% of the 2015 level. Consequently, the race is on to find new refrigerants for freeze-dryers before the supply runs out. Fortunately, an alternative is arising in some companies.
These topics and others will be discussed during the next PDA Europe Pharmaceutical Freeze Drying Technology conference at the end of November.
Learn more about the Pharmaceutical Freeze Drying Technology conference.
Disclosures: Thomas Beutler is Head of Liquid Dosage Application Development at GEA Lyophil GmbH, Hürth, Germany. Yves Mayeresse is Director of Manufacturing Science and Technology, Primary Process, Lean Process and Visual Center of Competency at GSK, Wavre, Belgium.