Millennials: How Manufacturers are Training the Next Generation
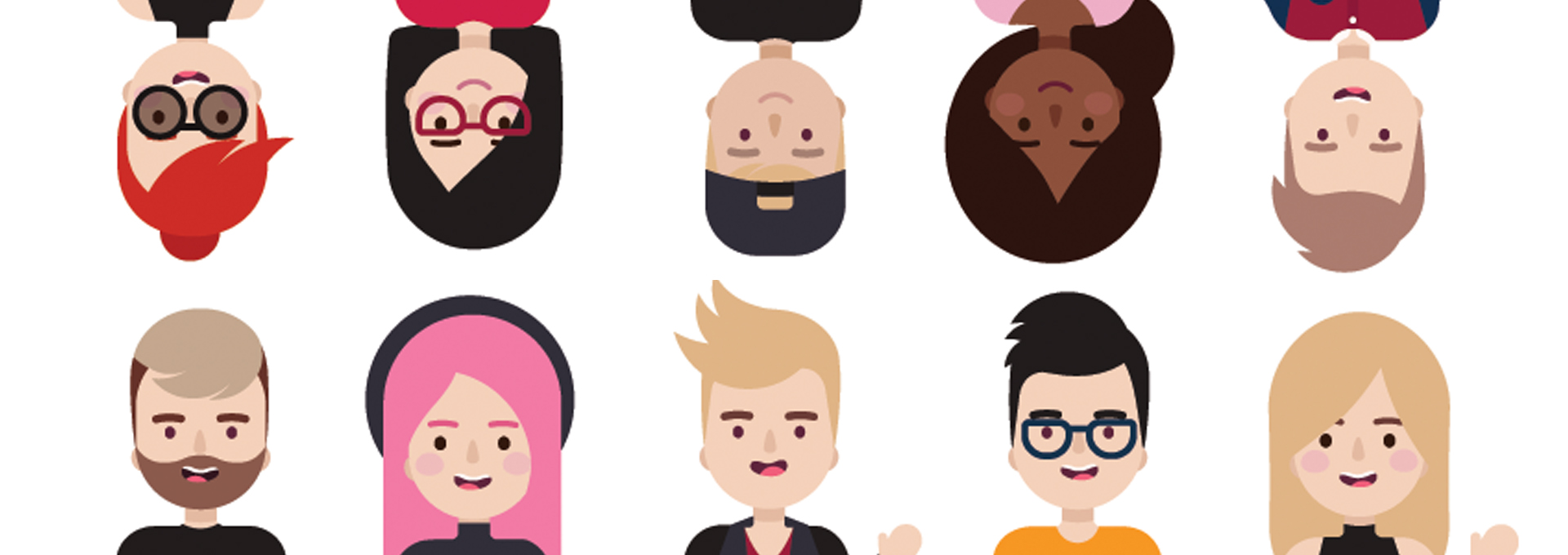
Millennials recently surpassed Generation Xers as the largest generation in the U.S. labor force (1). Defined by the U.S. Census Bureau as those born between 1982 and 2000, millennials came of age in a time of great technological change and economic uncertainty. It is no surprise that workplace survey after workplace survey show this generation seeks specific requirements in order to stay fulfilled at their jobs. Flexibility in when and where they work. Greater collaboration among colleagues. Ability to integrate technology into their roles. And companies that fail to deliver these requirements face the ever-present threat of their millennial employees seeking greener pastures, as they are more likely to switch jobs than other generations (2). This is not strictly a U.S.-only challenge for employers either; although fewer in number, European millennials also seek flexibility and emphasis on technology yet also remain open to other employment opportunities (3).