Keeping Biopharma’s Essential Services Lifeline Afloat during COVID
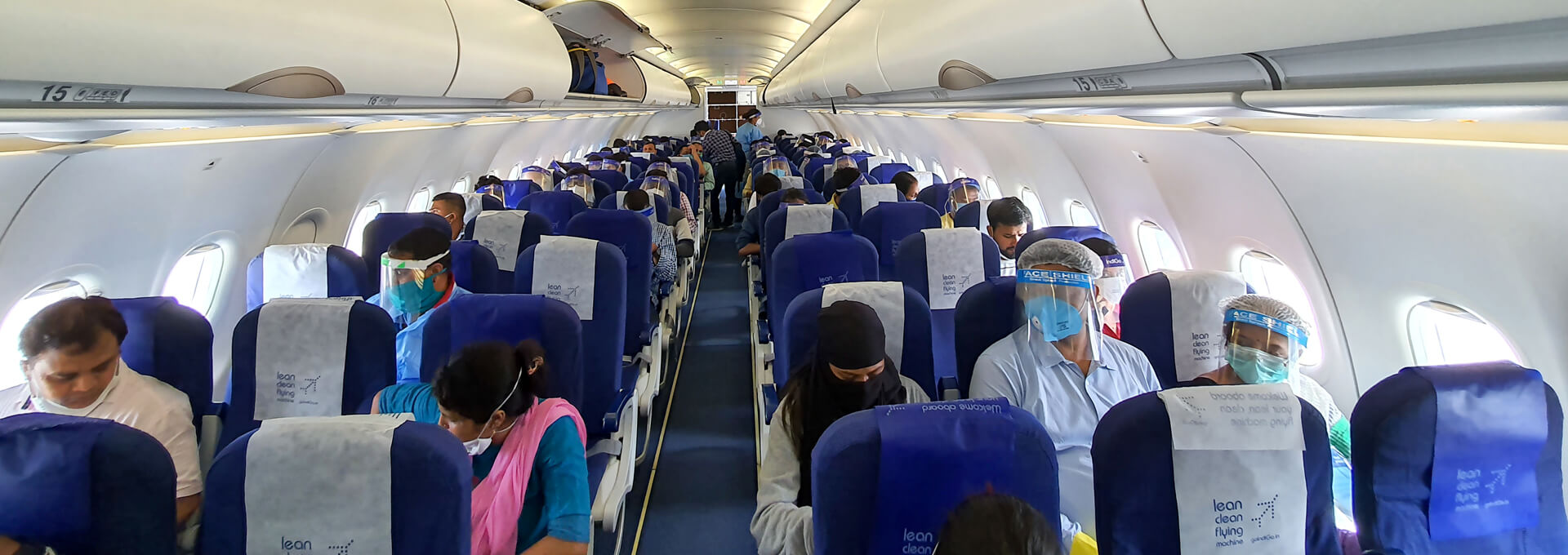
Whoever penned the term “essential services” should have included packaging material manufacturers, laboratory glassware suppliers, HVAC project engineers, and calibration service providers in the list. The lives of patients around the world depend as much on the continuity of operations of these supporting industries as they do on drug manufacturers.
When COVID-19 hit, many of these companies kept operations working with the help of remote access to the machines and other technology. Machine service engineers located overseas guided local service support online to help solve problems.
The most challenging questions that this industry had to quickly answer were:
- How do you set up an imported machine that needs technical support from the Original Equipment Manufacturer (OEM) with restrictions on international travels?
- How do you fix your most complex machine problems when they require a manufacturer’s intervention?
- Can you continue the smooth operations of production, R&D, or a QC laboratory with a broken-down supply chain of regular consumables?
The following case studies examine the challenges that the supporting industries unexpectedly faced and how they were overcome.
SCENARIO 1
Milieu: Pharmaceutical manufacturers, especially the ones racing to develop a vaccine for COVID -19, were in dire need of local as well as overseas engineers to complete the final stages of operational commissioning to enable production.
Challenges faced: It was to be a leap of faith, because time was the biggest challenge and synchronization of all actions from all quarters was a prerequisite. Having tests for COVID-19 performed, being issued test certificates, gathering tickets and travel gear and observing all the protocols for flying were indeed challenging, but not impossible.
Actions taken: Thanks to the network of contacts of these essential services industries, companies mobilized their resources to support their cause and ensure that the engineers were put on the “Vande Bharat Flights” (special flights to repatriate the overseas workmen). Armed with special permissions and express visas to arrive in time for the activities, all clearances and arrangements were made for their smooth transit into and out of the country. Precautions were taken for the assignment at hand, the well-being of teams from every angle was of the highest order.
Lessons learned: Travelling is a basic venture taken for granted, and business requirements necessitates it when subject matter experts are required to be on customer sites to erect, commission, repair or pull down the system or equipment. With the rules of quarantine in place, viability of travel and access to solving problems takes longer and costs escalate. The need to establish case- or person-specific quarantine rules instead of a general one-size-fits-all rule emerged.
The basic lesson learned is that, with due logic and applying common sense in the situation, workable solutions can be identified, planned and implemented. This pandemic is not going to end soon, and industry will have to fine tune its modus operandi to circumvent the hurdles accordingly.
SCENARIO 2
Milieu: The challenges faced by the regular manufacturing and laboratory consumable suppliers due to continued lockdowns in the country are related to on-time delivery of their products and services to the customers in pharmaceutical and biotech industry. Even after relaxation of the lockdown norms now, they continued to face challenges to serve customers due to sudden lockdowns or restrictions that are imposed by the local municipal authorities.
Paramjyoti Chakraborty, country head of BRAND Scientific Equipment, a leading laboratory instruments and consumables supplier in India, says:
“We are very much affected due to the lockdown norms. This has resulted in a cost escalation of around 25% in logistics apart from the increased cost of imports due to unavailability of passenger airlines helping in small cargo movements. So, for our products that qualify as premium products, especially for the pharmaceutical R&D and QC laboratories, we are left to bear this additional cost as a burden. Further, with limited cargo options on the international circuit, we are also forced to build up our inventories, since our customers working on various life-saving products can’t keep waiting for our products.”
Challenges faced: On-time delivery of the products and services at customer sites was most crucial. Due to various uncertainties, such vendors did not have enough time to plan their orders: either they received a sudden spike in demand, or they had inventories that remained on their shelves for weeks because of no demand.
“The transportation of instruments to the customer sites were nerve-wracking experiences due to the disruptions in supply chain and logistics services,” says Chakraborty.
Actions taken: The key actions involved increasing inventory-carrying norms, focusing on effectiveness of supply chain and introducing innovative approaches towards after-market services like product training and product service support, mostly through virtual means with limited physical presence by local resources.
Chakraborty explained, “To stay connected with our customers for our support, we are available on almost all online platforms based on customers’ choice. We have created product application videos for our customers that we use during the online meetings to demonstrate our products and we also provide virtual runs for some of our high-end products with inputs from our customers to their application requirements.
“On the internal side, we have updated our systems and continuously train all our team members with knowledge updates to deal with this changed scenario so that they can efficiently and seamlessly work with their customers, service providers and vendors.”
Lessons learned: The learning comes every hour and every day. Business agility with people, and the ability to shift gears with processes, is what will help sustain this industry in the post-COVID era.
Where do we go from here?
The next few quarters could remain as challenging as it has been for all ancillary businesses related to the biopharmaceutical and pharmaceutical industries, with shortages of the workforce, the uncertainty of demand, and the increasing cost of operations.
To maneuver through these choppy waters, first the business leaders of these industries must build better visibility of their entire system. This will come from adopting advanced technologies and digitizing their operations and supply chain networks. Next, efficiency in operations must be strengthened to meet the changing needs of the business and yet remain competitive. This would also call for building more of a regionalized structure than a global structure, investing in local talents, and ensuring the overall adaptability to these new business norms. The success of this entire ecosystem will depend upon the ability to co-create a business environment that will move towards a new patient-centric business model. Figure 1 depicts the path forward for ancillary industries.
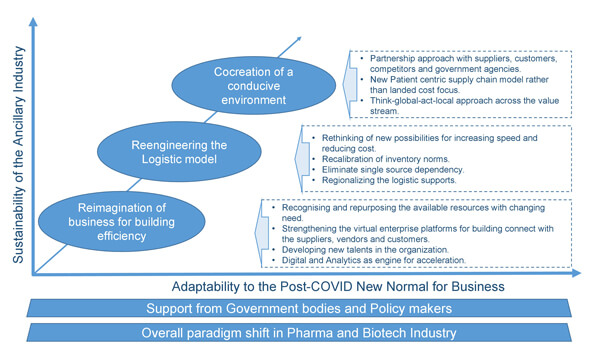
Conclusion
Indeed, these are turbulent times, but the bright side is the innate adaptability and resilience that businesses in the essential services have displayed to make things work.