How to Use QbD to Select Packaging Components
The development of a safe and effective drug product requires not only high quality ingredients but also careful selection of appropriate primary packaging components as these come directly into contact with the drug product. Interaction between primary packaging components and the drug product may result in failure to meet the quality target product profile (QTPP). This can be avoided by relying on a Quality by Design (QbD) approach.
Component Selection Using QbD
QbD is a systematic approach to development that begins with predefined objectives and emphasizes product/process understanding and process control. This approach should be based around sound science and quality risk management (QRM) (1). QbD can help establish a correlation between the material attributes of packaging components and quality of the drug product during the selection process for packaging components. The impact of each type of packaging component can be determined by monitoring certain quality attributes of the drug product. Table 1 presents the probable relationships between material attributes of packaging components and quality attributes of the drug product.
Table 1 Effect of primary packaging components on drug product attributes (√=Likely potential impact; X= Unlikely potential impact)
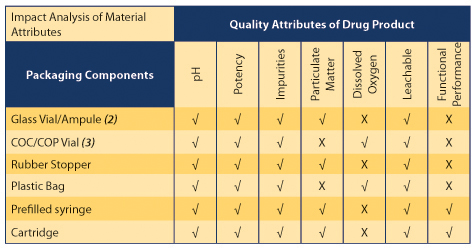
Figure 1 shows the QbD approach in detail. The most important step, when using the QbD approach, is identifying the Critical Quality Attributes (CQAs) of the drug product that can be affected by the material attributes of the packaging. In most cases, these CQAs consist of pH, potency, impurities, particulate matter, dissolved oxygen, leachables, and functional performance.
Figure1 QbD Approach Chart

After defining the CQAs, the Critical Material Attributes (CMAs) of the packaging components must be defined. These attributes include material of construction, size of container to fill volume ratio, and additional treatments, such as sterilization/depyrogenation, that can impact the CQA of the drug product.
Once the CMAs have been defined, the high-risk CMAs of the packaging components must be identified. These CMAs are further assessed based on a risk management approach. Risks can be classified based on probability and severity.
As an example, a hypothetical packaging component has the potential to interact with a drug product in the presence of light and heat. In this case, the severity is high. During initial development, data shows the component is incompatible with the drug product in the presence of light and heat. Thus, the probability of interaction between the drug product and the packaging component is also high. Therefore, the risk of using this packaging component is greater due to high severity and high probability.
Thorough experimentation/data or scientific justification should be provided to lower identified risks. To understand this step, consider again the hypothetical packaging component. Since it has been dentified as high risk, the component needs to be changed or additional controls on light and heat exposure to the drug product should be used.
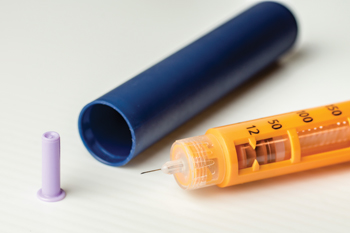
Enter the Design Space
Based on data from the experiments, design space should be established in order to minimize variability in drug product attributes due to the material attributes of packaging components. As per ICH Q8 Pharmaceutical Development, design space can describe the relationship between input variables (e.g., material of attributes) and process parameters demonstrated to provide assurance of quality. Working within the design space is not considered a change. For packaging components, design space can be generated by varying materials of construction, dimensions, processing conditions, oxygen permeability (in the case of semipermeable components such as cyclic olefin copolymer or plastic bags), etc. Design space is proposed by the applicant and subject to regulatory assessment and approval.
In the last stage of QbD, a control strategy must be defined as the set parameters of specifications for packaging components. The limits for all critical material attributes must be defined in the form of specifications and must be controlled in batch-to-batch manufacturing.
Conclusion
A QbD approach is a crucial consideration when selecting primary packaging components. Material attributes of packaging components should be considered to assess the impact on the quality of the finished product. Hence, QbD is an approach to mitigating risk associated with primary packaging and can be emphasized during the earlier stage of drug product development.
References
- Guidance for Industry: Q8(R2) Pharmaceutical Development, US Food and Drug Administration, November 2009
- Pillai, S., et al. “Pharmaceutical Glass Interactions: A Review of Possibilities.” Journal of Pharmaceutical Sciences and Research 8 (2016): 103–111.
- Markarian, J. “Plastic Shows Benefits in Parenteral Packaging.” Pharmaceutical Technology (December 19, 2012)