Dinner Meeting Addresses Virtual Companies, Preapproval Inspections
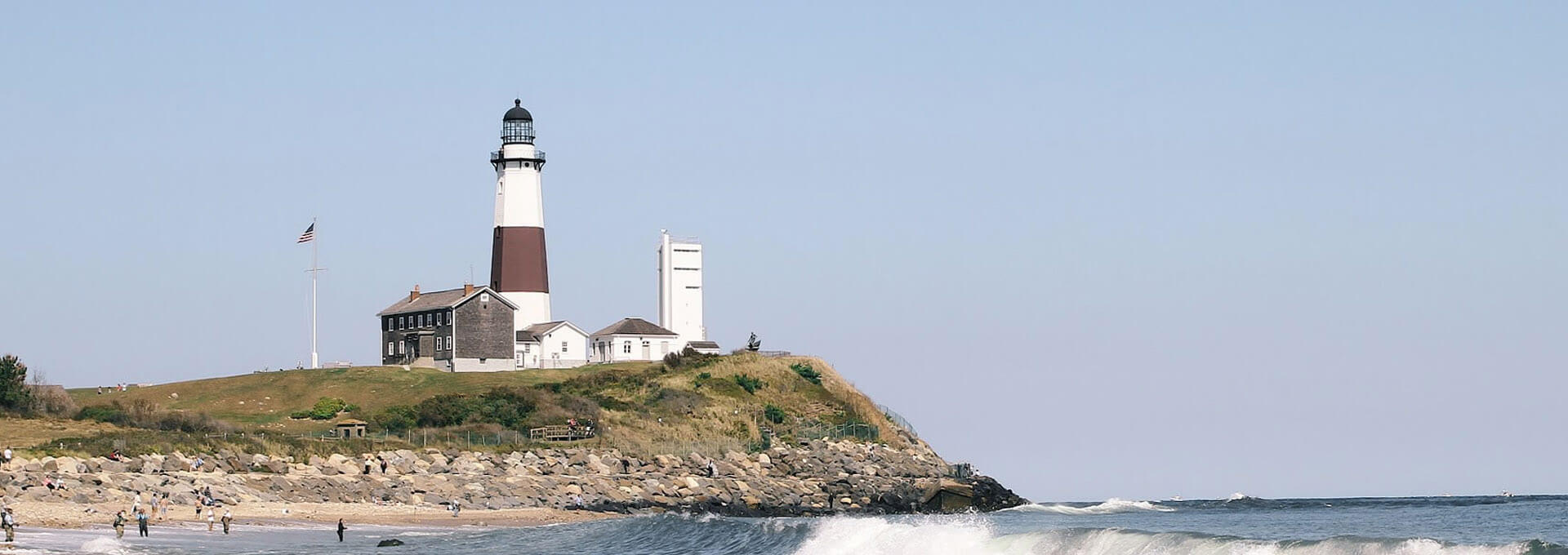
The PDA New England Chapter’s March 11 dinner meeting featured presentations from two speakers with U.S. FDA experience: former FDA official David Chesney and current Consumer Safety Officer Sean Marcsisin.
Chesney worked for many years with the FDA, in the Boston area and elsewhere, and is currently a consultant. In his presentation, “Quality and Compliance Management Issues – Virtual Companies,” he talked about the most common quality compliance concerns, that is, things that must be done to maintain GMP compliance, manage GCP compliance and handle FDA audits.
Chesney stated that understanding requirements applicable to the organization—GLP, GCP, GMP or a combination—is most important for regulatory compliance. He stressed that, for outsourced operations, virtual companies are ultimately responsible, even though operations are performed by CMOs, CROs, clinical trial sites or others. According to regulations, virtual companies must have a quality unit, and the release of final product must be performed in house, be it for clinical studies or commercial distribution. Since 2009, about 40% of FDA Complete Response Letters have resulted from CMC and GMP noncompliance, delaying approval of submissions and causing costly and time-consuming remediation—all of which could have been avoided.
He drew attention to the 2012 amendment of FD&C Act 501(a)(2)(B), which makes virtual companies responsible for the management of supply chain operations per GMP standards. This means virtual companies are responsible for vendor selection and raw material management, and they are required to establish SOPs or written procedures for these operations.
[Editor’s Note: Read an article David Chesney wrote on virtual companies published in the July 2018 PDA Letter.]
Chesney also discussed oversight of GCP operations by virtual companies. He pointed to situations where virtual companies assigned a quality leader with GMP experience. Yet GCP requirements are vastly different from GMP requirements which, for example, do not address patient safety, patient consent, clinical product inventory reconciliation or clinical site compliance. Thus, a quality leader with a GMP background may not be a good fit to manage GCP compliance. In these situations, Chesney recommends such a quality leader undergo basic GCP training.
Finally, he delved into FDA inspections, explaining that inspections are likely to occur after filing an NDA or BLA but before approval. Inspections may also be initiated “for cause,” such as issues with clinical trials or reports of adverse events after a product is marketed.
Next, Sean Marcsisin, provided a more in-depth look at FDA inspections, specifically preapproval inspections, in his presentation, “Dos and Don’ts of Pre-Approval Inspections: What to Expect When Being Inspected.” Marcsisin has been working in the FDA Office of Regulatory Affairs for four years. He serves as an investigator in pharmaceutical quality and as a subject matter expert on cGMPs for pharmaceuticals.
He explained that preapproval inspections are carried out to ensure the applicant can manufacture a drug at commercial scale and the submitted data are accurate and complete. In addition, inspections always assess the firm and/or facility’s overall conformance to cGMP. Marcsisin emphasized that not all sites require preapproval inspections; currently, FDA is using a new, risk-based model called an Integrated Quality Assessment to determine necessity.
Marcsisin offered a list of “do” advice that firms should consider. Always be prepared for an inspection whether one is expected or not. This includes ensuring there is a process in place for inspections, and personnel are primed to speak about their operational areas, including any known issues. He also recommended making sure facilities are clean and orderly, and all documents supporting operations are available. By taking these measures, firms can avoid what Marcsisin dubbed “SEMs” or “Severe Emotional Moments,” and increase the likelihood of a product manufacturing site being recommended for approval by the agency.
As to the inspection “don’ts,” the main takeaways are not to withhold or hide any information or engage in questionable practices with regards to data integrity.
All in all, what can a firm expect when being inspected? While there is variability in inspectors, for the most part, investigators are “nice guys.”
The New England Chapter thanks both speakers for their insightful and enjoyable presentations. A special thanks is also extended to meeting managers Brian Clark and Louis Zaczkiewicz; Steve Jones, Communications Chair, for generating chapter membership communications; Mark Gindi who processed registrations; John Masiello for photographing the event; and to all the volunteers who helped before, during and after the event. Their support is invaluable to the success of the chapter and is much appreciated!
PDA Who's Who
- David Chesney, Principal and General Manager, DL Chesney Consulting
- Brian Clark, Principal Consultant, GMP Operations Consulting
- Mark Gindi, text
- Steve Jones, Manager, Validation Support, and President-Elect, PDA New England Chapter
- Sean Marcsisin, PhD, Consumer Safety Officer, FDA
- John Masiello, Executive Vice President, Masy Bioservices
- Louis Zaczkiewicz, GxP Quality Consulting