Balancing Act: Human vs. Machine Inspection in Pharmaceutical Manufacturing
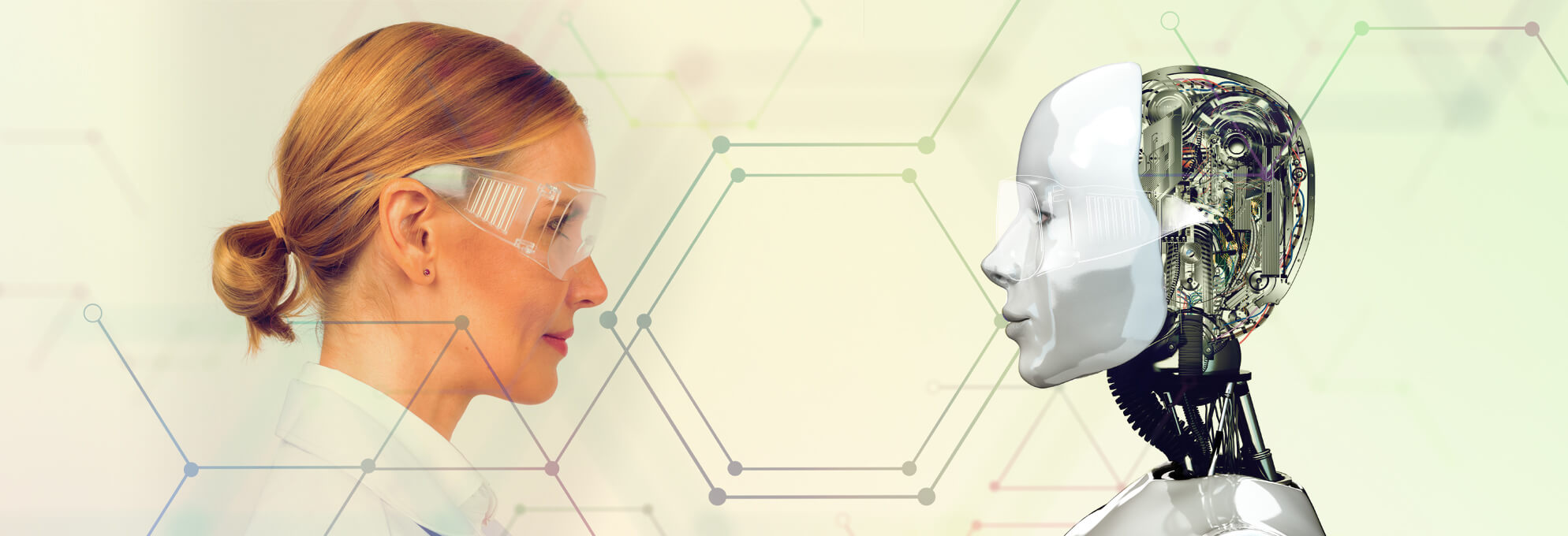
In the fast-paced and exacting realm of pharmaceutical manufacturing, the pursuit of precision, safety, and efficiency has never been more paramount. For visual inspection of parenteral products, two formidable forces have emerged as contenders for supremacy in ensuring the highest quality: The meticulous discernment of human inspection and the unyielding precision of machine inspection. As pharmaceutical manufacturers navigate the delicate balance between tradition and innovation, they face a pivotal question: How do they harmonize the capabilities of human inspectors with the relentless accuracy of automated systems?
In my exploration of this intriguing conundrum, I embark on a journey through the world of pharmaceutical manufacturing, seeking to unravel the intricate dynamics of the "Balancing Act: Human vs. Machine Inspection in Pharmaceutical Manufacturing." Join me, as I delve into the intricacies of this critical industry and the compelling dialogue surrounding the roles played by human expertise and automated technology in safeguarding the health and well-being of millions.
Pharmaceutical drug products undergo rigorous inspection processes before they are labeled. This inspection ensures that the drug product containers meet predefined specifications for container/closure integrity and that the drug product is nearly devoid of visible particulate matter.
In the realm of sterile pharmaceutical drug manufacturing, the traditional approach to visual inspection has long relied on the expertise of human inspectors. This time-honored method involves skilled professionals meticulously scrutinizing drug product containers for various defects, including visible particulate matter and container/closure integrity issues. The primary goals of post-filling and sealing inspections are to confirm that the container/closure is devoid of defects that might compromise sterility and that the drug product inside is devoid of visible particulate matter. The United States Pharmacopeia (USP) Convention requires visual inspection of all products intended for parenteral administration (1).
Human inspectors play a pivotal role in visual inspection, offering a range of advantages that stem from their adaptability, experience, and nuanced decision-making abilities. Their adaptability shines through in their capacity to navigate complex and dynamic work environments. Human inspectors can readily adjust their inspection processes to suit changing conditions, product types, or emerging defects, ensuring a flexible and responsive approach to quality control.
Years of experience further empower these professionals, providing them with a deep well of knowledge gained from encountering diverse products, defects, and manufacturing scenarios. This experience equips them with a keen eye for subtle variations and anomalies that automated systems might overlook. In essence, the adaptability, experience, and nuanced decision-making prowess of human inspectors collectively contribute to their indispensable role in upholding product quality and safety across various industries.
Traditional 100% manual inspection for visible particulate matter and defects is slow and labor-intensive, unsuitable for high-volume production. To meet high-volume production inspection needs, pharmaceutical companies are turning to automated vision systems.
Rise of the Machines
In the modern context, automated inspection systems use arrays of cameras and vision software to examine sealed containers. Machine vision engineers develop tailored vision algorithms, while AI and machine learning enhance defect detection. AI systems learn from vast image datasets, identifying subtle defects and offering real-time analysis, reducing errors. This integration improves accuracy, reliability, and supports predictive maintenance and production optimization in modern manufacturing.
Automated visual inspection offers speed, precision, and consistency advantages. It quickly processes large volumes, excels in detecting tiny defects, and ensures uniform quality without fatigue or distractions. This is crucial in industries valuing consistency and strict quality standards, enhancing efficiency and product integrity.
Human inspectors, while skilled, are susceptible to limitations in visual inspection within pharmaceutical manufacturing. Fatigue can set in during prolonged and repetitive tasks, diminishing concentration and observation capabilities.
Subjectivity is inherent in human perception, leading to variations in defect detection and classification among inspectors. For instance, in 2012, the U.S. FDA discovered that human inspectors at the New England Compounding Center failed to identify contaminated steroid injections, leading to a multistate outbreak of fungal meningitis that resulted in several deaths and illnesses (2). These limitations underscore the need for complementary automated inspection systems to ensure consistent and precise quality control in pharmaceutical manufacturing.
While automated vision inspection (AVI) systems effectively address issues connected with manual inspection, their performance can be hindered by programming limitations. If the system is programmed to account for every possible variation in inspection conditions, it may erroneously flag safe products as defective (3). Furthermore, practical constraints affect the widespread implementation of these systems in all operational scenarios. Numerous contract development and manufacturing organizations (CDMOs) encounter challenges when justifying the significant capital investments and the associated validation processes, particularly when dealing with products produced in small batches or those with infrequent production cycles (4).
Man and Machine Together
In pharmaceutical manufacturing, successful examples of human-machine collaboration in visual inspection are becoming increasingly prevalent and impactful.
Automated visual inspection systems, equipped with advanced machine learning algorithms and high-resolution cameras, work in tandem with human inspectors to enhance efficiency and precision. These systems can rapidly scan large batches of pharmaceutical products, flagging potential defects with remarkable accuracy.
Human inspectors, in turn, apply their expertise to make nuanced decisions, particularly when assessing complex or ambiguous cases. This collaborative approach harnesses the strengths of both human cognition and machine speed and consistency, ensuring that pharmaceutical manufacturing maintains the highest standards of quality and safety while optimizing production efficiency.
AI-driven vision systems play a crucial role by conducting initial inspections to detect defects and provide detailed information about the nature of these defects, such as identifying bubbles and identifying potential contaminants like hair (see Figure 1). While these systems excel at tasks like measuring surface area, they face limitations when it comes to assessing weight, which is a critical factor in determining the pass or fail status of safety-critical pharmaceutical products. This is where human expertise comes into play in collaboration with AI. Humans are responsible for defining the specific features and criteria that dictate whether a product passes or fails inspection, ensuring a comprehensive and reliable quality control process (5).
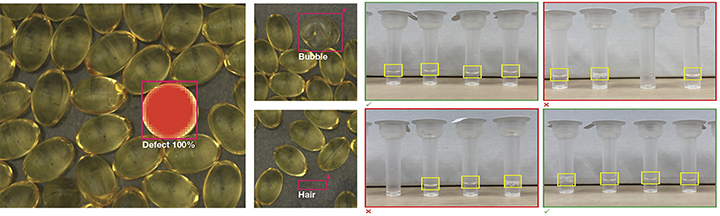
The global inspection machines market was valued at $721 million in 2022 and is expected to reach $905 million by 2027 with a 4.7% compound annual growth rate (see Figure 2). Factors driving this growth include increased adoption of automated inspection systems in pharmaceutical and biotech, more inspection checkpoints, and technological advancements (6).
A research project at the University of Waterloo and University of California – LA (UCLA) introduced Human–Machine Collaborative Inspection (HMCI), combining Mixed Reality (MR) headsets and a robot for structural inspections. This system empowers inspectors to enhance results from automated defect detection algorithms in real-time, utilizing 3D maps and image data collected by the robot and processed by a computational server, then overlaid onto the MR headset for inspection (7).
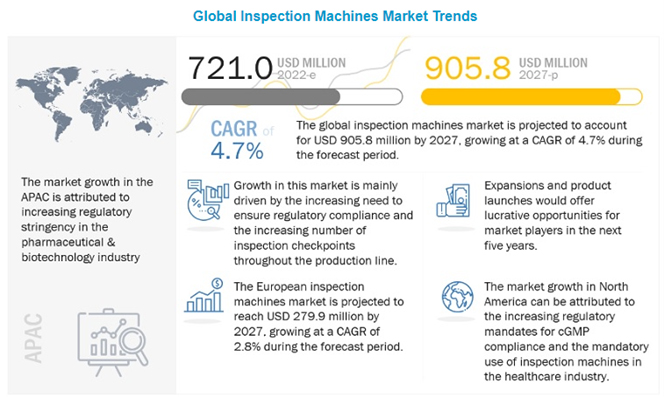
AI Faces FDA & EMA Challenges
AI faces barriers to widespread adoption due to challenges in obtaining liability insurance and regulatory approval.
The regulatory landscape for inspections is changing, with agencies like the FDA and EMA recognizing automation's potential (8,9). Adhering to evolving standards, including risk-based approaches and data integrity, is crucial for product safety and regulatory approval. Manufacturers must follow GMP and adapt to new technologies like AI. Global harmonization efforts aim to simplify compliance for companies operating in multiple regions. Staying compliant with changing standards is essential for pharmaceutical manufacturing's product quality and regulatory adherence.
In the ever-evolving landscape of pharmaceutical manufacturing, the synergy between human expertise and machine precision emerges as a critical imperative. As we have explored the advantages and limitations of both human and machine inspection methods, it becomes evident that achieving the highest standards of safety and quality in pharmaceutical products necessitates a harmonious collaboration between these two entities. The discerning eye of the human inspector, with its adaptability and nuanced decision-making, remains irreplaceable, while automated systems excel in speed, consistency, and data analysis. The question that lingers, as we gaze into the future of inspection in pharmaceutical manufacturing, is not one of choosing between human or machine, but rather how we can optimize this partnership further. How can we leverage emerging technologies, refine regulatory frameworks, and empower our workforce to harness the full potential of human-machine collaboration? It is in this ongoing quest for excellence that the future of pharmaceutical inspection holds both challenges and boundless opportunities, all in the pursuit of safer, more reliable, and higher-quality pharmaceutical products.
References
- “USP General Chapter: Visible Particulates and Injections.” In United States Pharmacopeia. Rockville, MD: USP Convention, 2017.
- New England Compounding Center Pharmacist Sentenced for Role in Nationwide Fungal Meningitis Outbreak.
- Vision Inspection Using ML/AI.
- https://www.ncbi.nlm.nih.gov/pmc/articles/PMC3066354/#
- AI Streamlines Inspection in the Pharmaceutical Industry.
- https://www.marketsandmarkets.com/Market-Reports/inspection-machines-market-81453085.html
- Z.Al-Sabbag, C. Yeum, S. Narasimhan, Enabling human-machine collaboration in infrastructure inspections through mixed reality, Adv.Engg.Informatics, Volume 53, August 2022, 101709.
- Artificial Intelligence Discussion Paper (fda.gov)
- Reflection paper on the use of artificial intelligence in the lifecycle of medicines | European Medicines Agency (europa.eu)