Achieving Top Management’s Interest Through the Use of KPIs and QPIs
Key performance indicators (KPIs) are specific, measurable and quantifiable metrics that are used to evaluate the performance of a particular process or system. They are often used to monitor the efficiency and effectiveness of key business functions, such as production, sales, marketing and customer service. In the pharmaceutical industry, for example, KPIs can include the following:
- Production yield — Percentage of finished products that meet the required quality standards
- Cycle time — Time it takes to complete a specific process, such as drug manufacturing
- Market growth — Percentage increase in sales or agreements revenue over a specified period
- Customer satisfaction — Percentage of customers who are satisfied with the products provided
KPIs are indicators of significant interest, but how effective are they in the pharmaceutical industry for measuring quality?
From a quality standpoint, if we reduce performance analysis to only the measurement of KPIs, we will have a biased analysis, one that is less effective and with less focus on improvement than if we evaluate KPIs in conjunction with quality metrics.
Quality metrics or quality performance indicators (QPIs) are specific indicators used to monitor and assess the quality of pharmaceutical products and processes. They are used to ensure that products meet the required quality standards and to identify any areas for improvement. In November 2016, the U.S. FDA issued a draft guidance document called the Submission of Quality Metrics Data Guidance for Industry that defined the following three major quality metrics:
- Lot acceptance rate — Indicating manufacturing process performance
- Product quality complaint rate — for patient or customer feedback
- Invalidated out-of-specification (OOS) rate — indicating the operation of a laboratory
Evolution of quality metrics in recent years
In March 2017, the International Society for Pharmaceutical Engineering (ISPE) responded to the FDA’s 2016 draft guidance on metrics Request for Comments Notice in the Federal Register, submitting an extensive and detailed response (See Figure 1). These data-driven comments were informed by the following:
- Four years of work with industry leaders and experts by the ISPE Quality Metrics Core Team
- Two pilot programs, involving 28 companies and 83 sites
- An interactive workshop with 22 pharmaceutical companies participating
ISPE members and FDA continue to focus on developing guidance. What has become clear, however, is that the quality metrics should be used internally within companies to drive and improve quality standards.
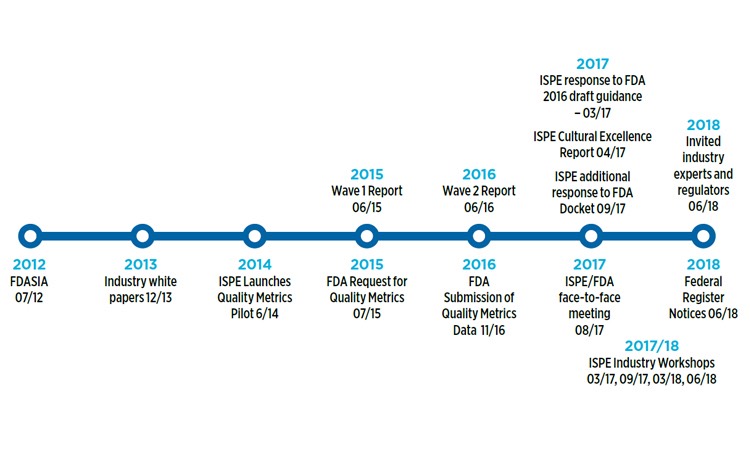
Overall, what should be emphasized is that the interest of company directors tends to be better measured through KPIs, while the interest of the quality department is better measured through QPIs. This leads to the question of what strategy can we use to interrelate KPIs and QPIs to articulate a company’s top management objectives with quality objectives?
A proposal should be made to implement a strategy of a quantifiable breakdown of each of the KPIs in one or more QPIs to develop a corporate quality policy from the top executive management. Also, the proposal should stimulate the allocation of resources and investment flow in points that we consider important from the quality point of view, often seen as an expense rather than an investment by business executives.
In summary, we can consider the management and increase of the KPIs through the management and increase of each of the QPIs that comprise it. Therefore, interrelating KPIs and QPIs is a strategy that encourages a change in corporate focus toward quality and fosters continuous improvement, technological development and process optimization. This would allow for cleaner and more controlled processes that prevent quality risks and economic consequences. This is achieved through developing a robust quality management system that involves:
- Skilled and trained work teams
- An optimized risk management system
- Serious and effective CAPAs
- Continuous improvement and optimization of processes
- Robust supplier evaluation
- Increased technological innovation in facilities and equipment
- Adequate computerized systems
Case study
Here, for example, are one of the multiple KPIs reported annually by a pharmaceutical manufacturing company engaged in the production of sterile parenteral drugs in Canada.
- KPI 1 — Batch performance: Percentage of batches meeting the required quality standards in one year.
This KPI can be broken down into multiple QPIs, of which, for practical purposes of explaining the analysis method, we will continue to analyze only one of them, for instance:
- QPI 1 — Physicochemical OOS: Number of batches rejected for OOS of critical physicochemical parameters in a year.
We can prospectively (or preventively) analyze this QPI into the different QPIs that compose it, such as:
- QPI 1.1 — Rework or reprocessing due to a physicochemical issue: Batches of critical physicochemical parameters approved but as a result of rework or reprocessing due a physicochemical issue in one year.
- QPI 1.2 — Physicochemical OOT: Batches with critical physicochemical parameters within specification but out of trend (OOT) in one year.
At the same time, we can perform the same breakdown by a retrospective (or corrective) analysis based on the root cause of this QPI, assuming that the root cause of this OOS, for instance, is the expiration of the scale recalibration:
- QPI 1.3 — Noncompliance within the ACQP: Number of noncompliances within the annual calibration and qualification plan (ACQP) during that year.
Through this debottlenecking strategy, we are in a position to mitigate a negative KPI retrospectively and prospectively. In addition, we can find anchor points from which we can work from quality to offer top management a proposal to improve the initial values of the KPI.
By linking a deficient/low KPI with one or more deficient/low QPIs that originate it, we close the interest gap with top executive management and help put quality at the fundamental epicenter of the laboratory’s corporate policies. Moreover, this will undoubtedly help us to have more resources to stimulate the flow of investments to the sector, which is often a major limiting factor for the growth and development of the area.