5 Steps of Design Thinking
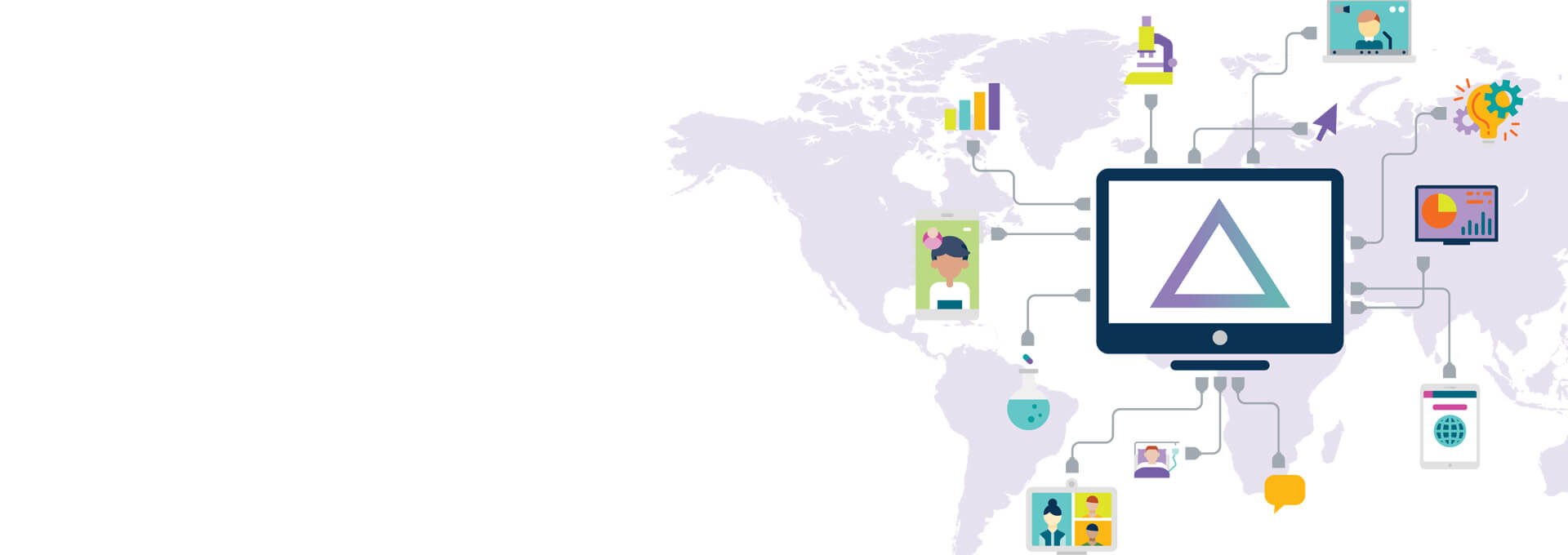
“Design Thinking in quality is no longer business as usual,” rang the opening volley of Huiling Loo, Head of Quality Systems and Validation, Roche Singapore Technical Operations.
In her presentation, “Breakthrough Ideas in Quality, Design Thinking Approach,” at the PDA 2020 Virtual Annual Meeting, she explained how pharma needs to change the way it thinks about designing quality systems to keep in step with the rapid changes in technology.
Loo said current methods are too complex, highly reactive, compliance- versus customer-focused, and risk adverse. The norm is “business as usual is good enough.” Pharma needs to reimagine a new quality system that will meet the needs of personalized healthcare, advanced therapies and new technologies. The Design Thinking approach involves transformative change, which she likened to building a house on empty piece of land, as opposed to transitional change, improving a house through renovation.
Design thinking comprises five steps, according to Loo:
- Empathize
- Define
- Ideate
- Prototype
- Test
Design thinking requires a shift in mindset (empathize) that Loo described as, “I see, I listen, I experience.” She used the Apple IPhone as an example, saying, “Apple didn’t need to make the phone smarter, but found out what people would need.” To be innovative, pharma needs to learn what patients need, find new ways to meet those needs, “think big,” put those thoughts into actions, and then test them out.
Loo experimented with applying design thinking to two quality processes, discrepancy management and technical change management, and compared them to standard methods. Collaboration is fundamental, but many take a conservative approach to problem-solving because it is safe and familiar, which results in processes that are too complex. Design management process would focus on user requirements (simple, fit for purpose) and insight (no standard work or silo working), would redefine the process (minimum requirements, risk-based) and create collaboration tools, and then would test those processes with pilot runs.
By following “what do we fix first?” and using the low-risk deviation experiment, Loo’s team closed events faster (by 50%) because they focused on the issue and worked directly together to make changes happen quickly. The technical change management redesign experiment examined which change records involved minor changes and created a standard checklist to evaluate them. Through that they determined the change record route would not be followed if there was no impact to product quality, validation, regulatory or third-party issues or interdependencies, reducing the number significantly.
Loo closed by identifying the challenges to applying design thinking to quality systems. The skillset needed is vastly different, which requires a strong quality culture and an innovation-minded organization. And, while speed is often more important, she said, the idea of “one batch, one patient,” gives a whole new meaning to “right first time.”