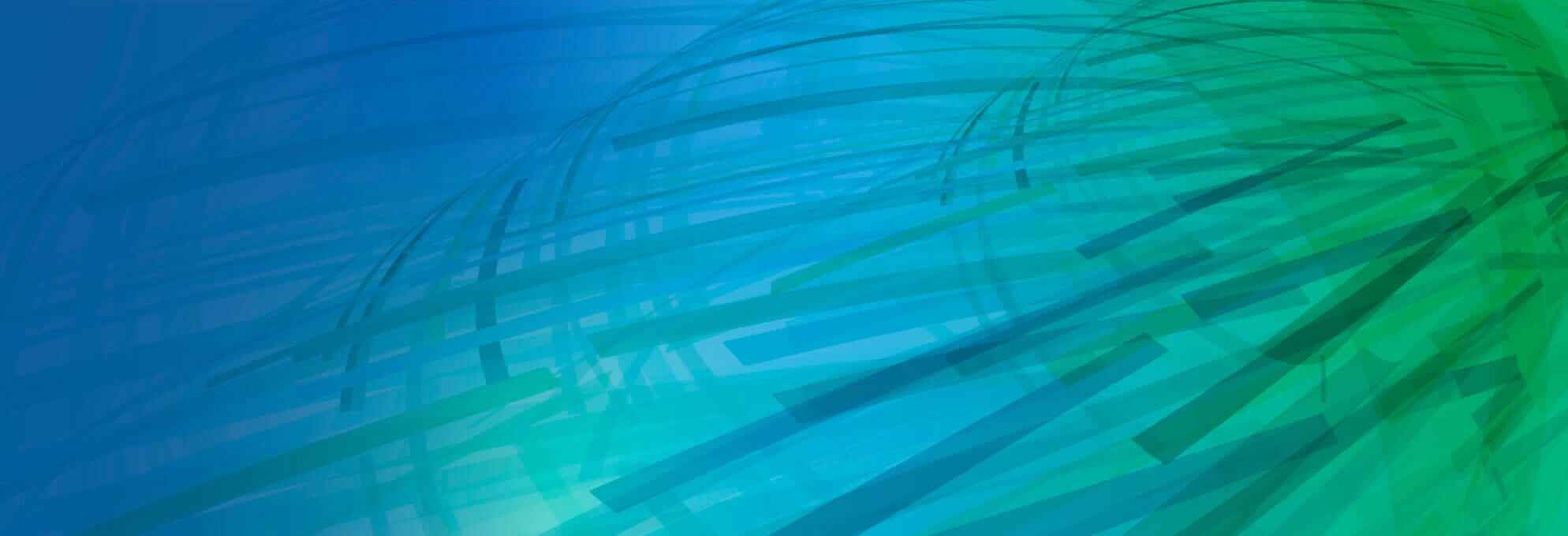
Quality Risk Management for Facilities and Equipment
Registration Options
Individual Registration
Group Registration
Time: 8:30 a.m. - 4:00 p.m.
Facilities and equipment represent one of the six major segments of the Quality System identified by the FDA as areas of focus for GMP inspections. They represent the major capital cost associated with drug substance and drug product manufacture.
In addition to associated financial value, facilities and equipment are critical to establishing and maintaining product quality by ensuring process, environmental and material control. Associated risks must be understood and controlled in order to reliably achieve product quality.
Over the course of the asset life-cycle, different risks may be recognized and assessed. Control or mitigation strategies at each stage of the life-cycle are essential to continuous delivery of a quality product.
This course will explore the application of risk-based strategies to most effectively manage the entire life-cycle of facility and equipment assets in GMP manufacturing. Discussions will begin with design and the relationship of facilities and equipment to product quality. It will progress through the entire life-cycle from start-up, qualification, operation, maintenance and, finally, to retirement.
Emphasis will be placed on rationale for determining risk and methodology to control or mitigate it. Focus will be directed toward real risk to product quality and the application of best practices to ensure both technical control and oversight by the Quality unit. Regular re-evaluation and continuous improvement will be discussed.
The course will be lecture-based and will be structured to provide an open and interactive environment wherein all participants will contribute to the learning experience of the entire group.
Who Should Attend
The following individuals will benefit from this course:
- Engineering and maintenance professionals responsible for the design, construction, commissioning, qualification and asset life-cycle management of GMP manufacturing facilities and equipment
- Validation and technical experts responsible for overseeing and advising on GMP design and qualification requirements
- Quality assurance personnel responsible for reviewing, approving and overseeing quality systems associated with facilities and equipment
- Personnel responsible to operate and monitor production facilities and equipment
Event Location
Contact
Program Inquiries
Training Course Inquiries
Registration Customer Care
More information coming soon.
Day 1
Upon completion of this course, you will be able to:
- Identify the relationship between facility and equipment design and the critical quality attributes of a product
- Assess risk to quality (and other risks) arising from facility and equipment
- Develop methodology to quantify and mitigate facility and equipment risk to quality, as well as to safety, the environment and to the business objectives of the company
- Apply risk-management tools in order to direct the focus of general quality systems (e.g., change control, deviation management, documentation practices) toward significant risk to quality
- Describe the application of equipment specific quality systems (e.g., maintenance, calibration, equipment qualification) to ensure quality
Continuing Education for Pharmacists
PDA is accredited by the Accreditation Council for Pharmacy Education (ACPE) as a provider of continuing pharmacy education. Participants may sign up to receive Continuing Pharmacy Education (CPE) credits. To do so, participants must sign in at the beginning of the program, submit the provided evaluation forms and mail the CPE credit request to the address stated on the form. Attendees must be present at the full event to receive Continuing Pharmacy Education credit, which will be awarded as follows:
PDA #467 | ACPE #0116-0000-15-028-L04-P | 0.6 CEUs
Type of Activity: Application
Continuing Education for Professional Engineers
New Jersey
PDA is an approved provider by the New Jersey State Board of Professional Engineers and Land Surveyors to offer courses to New Jersey Professional Engineers for Continuing Professional Competency (CPC) credit. Following the full participation in this course, participants will receive a Certificate of Accomplishment specifying the number of CPC credits that may be awarded. This certificate can be submitted as verification of completion to the Board for license renewal.
The credit value of this course is 6 CPC credits.
North Carolina
PDA is recognized by the North Carolina Board of Examiners for Engineers and Surveyors as an Approved Sponsor of Continuing Professional Competency (CPC) activities for Professional Engineers licensed by North Carolina. To receive a Certificate of Accomplishment specifying the number of Professional Development Hours (PDHs) that may be awarded, course participants must request the North Carolina Board of Examiners evaluation form from PDA staff. This form must be completed onsite at the conclusion of the course and returned to PDA staff.
The credit value of this course is 6 PDHs.
Become a Sponsor
Interested in becoming a sponsor? Learn about opportunities and benefits.
Request InformationBecome an Exhibitor
Interested in becoming an exhibitor? Learn about opportunities and benefits.
Request InformationPLEASE READ PDA is not affiliated or contracted with any outside hotel contracting company. If someone other than PDA or the PDA chosen hotel contacts you suggesting that they represent any PDA event, they do not. It is PDA's recommendation that you book your hotel directly through the official PDA chosen hotel that is listed on our web site.
PDA Training and Research Institute
4350 East West HighwayBethesda, MD , United States
Phil DeSantis, Principal, DeSantis Consulting Associates
Phil DeSantis is a pharmaceutical consultant, specializing in Pharmaceutical Engineering and Compliance. Phil retired in 2011 as Senior Director, Engineering Compliance for Global Engineering Service at Merck (formerly Schering-Plough) located in Whitehouse Station, NJ. His responsibilities included development, implementation and support of standards and practices for all facility and equipment-related capital projects and site operations. He served as Global Subject Matter Expert for Facilities and Equipment and on the Global Validation Review Board and Quality Systems and Standards Committee.
Phil is a chemical engineer, having received a BSChE from the University of Pennsylvania and an MSChE from New Jersey Institute of Technology. He has over forty-five years of pharmaceutical industry experience. Prior to Schering-Plough, Phil held executive positions for Fluor Corporation and Raytheon Engineers & Constructors, where he led groups providing validation and compliance consulting services to pharmaceutical and biotech clients. Prior to that, he served in technical positions in several major pharmaceutical firms, including Squibb, Ortho Pharmaceutical Corporation and an earlier period at Merck. He is on the PDA Scientific Advisory Board and is active in ISPE. He has been as a frequent lecturer for both organizations. He has published or contributed to several articles and books in the area of validation and pharmaceutical engineering. In addition, Phil has lectured on "Steam and Dry Heat Sterilization" as part of the FDA's field investigator training program.