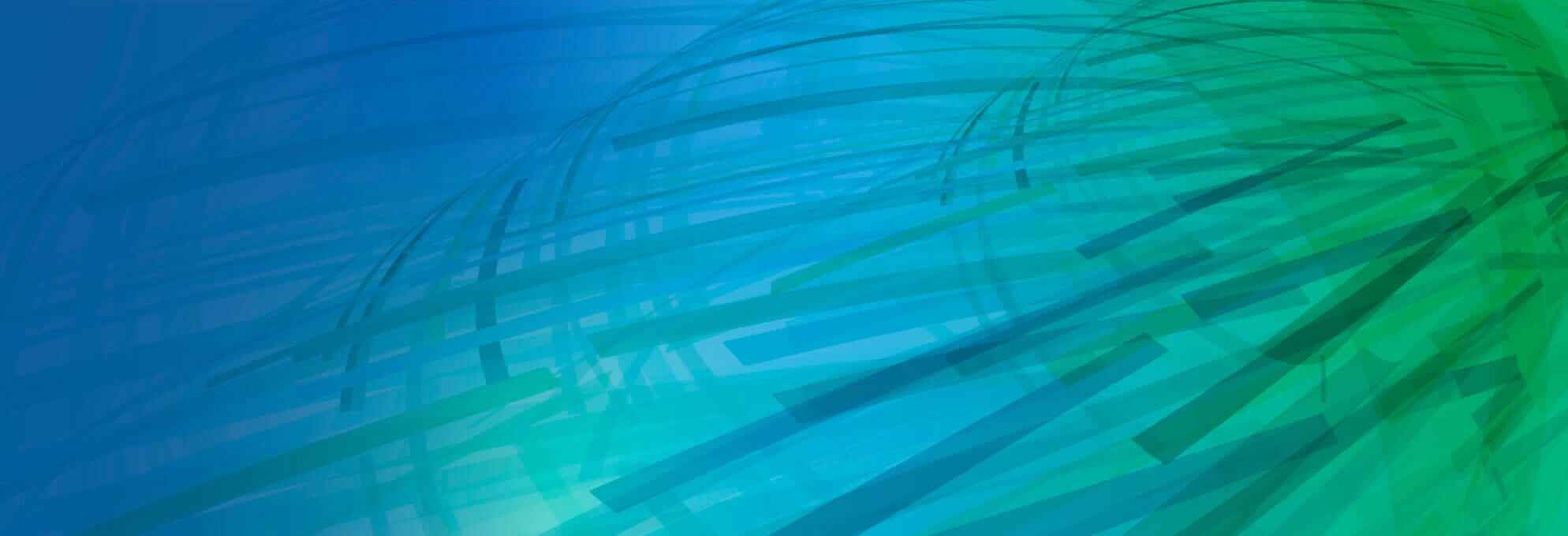
QRM Application
Registration Options
Individual Registration
Group Registration
Duration: 4 days
Time: 8:30 a.m. - 4:00 p.m.
Course 1 Title: Foundations of Quality Risk Management
This course will provide an overview of the Quality Risk Management (QRM) process with an emphasis on the principles in ICH Q9 and ICH Q10. A portion of the course will be focused on how QRM can be integrated into the Pharmaceutical Quality System and the use of QRM principles throughout the product lifecycle. The course will further build on the conceptual lessons, by teaching practical skills, covering a broad look at QRM tools, templates, facilitation tips, and managing teams and bias. Lastly, this course will close out with evaluating the power of decision making in using a risk register and a best practice approach for building a QRM program at your company.
Important Note
This course is an updated version of a prior PDA course, “Implementation of Quality Risk Management for Pharmaceutical and Biotechnology Manufacturing Operation.” Please note that the content of both courses is similar. If you have already taken “Implementation of Quality Risk Management for Pharmaceutical and Biotechnology Manufacturing Operation,” we recommend that you consider taking “Foundations of Quality Risk Management” only as a refresher.
Course 2 Title: Practical Application of Quality Risk Assessment Tools
This course will cover application of various quality risk assessment tools and considerations for tool selection. Different case studies from drug substance manufacturing and packaging and labeling will be used to demonstrate application of the various tools.
Learners will understand how to apply the formality spectrum for tool selection and learn where simpler risk assessment tools can be more useful instead of detailed tools. They will also learn how different tools can be applied in combination to address a risk question.
Additionally attendees will get hands-on practice with the more detailed and structured risk assessment tools - PHA, FMEA and FTA as follows. In each of the application case studies all stages of the QRM process will be covered including identification of risks, risk controls, estimating residual risks, practicing documentation and communication of outcome to management, and obtaining approval from decision makers.
- First, learners will practice performing a preliminary hazard analysis (PHA) to identify hazards, harms, and hazardous situations associated with a proposed protein drug substance packaging suite, and a bottling and packaging operation of oral non-sterile liquid product.
- Second, learners will perform a failure mode and effect analysis (FMEA) to assess the potential product quality risks associated with a protein A chromatography process, and a secondary packaging components production process. Application of FMEA will include identifying specific failure modes, failure effects, and cause of the failures associated with potential risks during manufacturing and packaging.
- The third case study involves use of the fault tree analysis (FTA) to identify and assess potential product quality risks, specifically with a virus contamination event in cell culture, and packaging, handling and transport of liquid filled glass syringe.
Prerequisites: Participants enrolling in this course must have completed one of the following PDA courses:
- “Foundations of Quality Risk Management” taking place Monday, December 11, 2017 at the PDA Training and Research Institute in Bethesda, Maryland.
- Any offerings of the prior PDA course, “Implementing Quality Risk Management for Pharmaceutical and Biotechnology Manufacturing Operations.”
Additionally, participants should have read PDA Technical Report 54 (TR 54), Implementation of Quality Risk Management for Pharmaceutical and Biotechnology Manufacturing Operations.
Who Should Attend
The QRM Application track includes two courses: “Foundations of Quality Risk Management” and “Practical Application of Quality Risk Assessment Tools.” This training module is applicable to pharmaceutical professionals engaged in QRM application activities related to chemistry, manufacturing and controls for pharmaceutical and biotechnology processes. This includes: manufacturing supervisors/managers/directors, process development biochemists, microbiologists, cell biologists and molecular biologists, process engineers, quality assurance professionals, regulatory CMC supervisors/managers/directors, quality control and analytical development professionals.
Event Location
Contact
Program Inquiries
Training Course Inquiries
Registration Customer Care
More information coming soon.
Day 1
Course 1 Title: Foundations of Quality Risk Management
Upon completion of this course, you will be able to:
- Describe the Quality Risk Management (QRM) process and explain the roles and responsibilities
- Describe when, where and how to apply risk management throughout the product lifecycle
- Plan and prepare for quality risk management activities
- Describe the formality associated with QRM tools
- Describe the purpose of a risk register
- Build a QRM program at your company
Course 2 Title: Practical Application of Quality Risk Assessment Tools
Upon completion of this course, you will be able to:
- Apply the formality spectrum concept for risk assessment tools
- Explain why and how tool selection is important in ensuring the right outcomes and decisions from a QRM application.
- Examine considerations when selecting the appropriate risk assessment tool
- Demonstrate where and how application of simple risk assessment tools such as checklists, simple decision trees, technical assessments etc. can be used as alternatives to more detailed risk assessment tools such as PHA, FMEA, FTA
- Use structured risk assessment tools such as PHA, FMEA and FTA
Continuing Education for Pharmacists
PDA is accredited by the Accreditation Council for Pharmacy Education (ACPE) as a provider of continuing pharmacy education. Participants may sign up to receive Continuing Pharmacy Education (CPE) credits. To do so, participants must sign in at the beginning of the program, submit the provided evaluation forms and mail the CPE credit request to the address stated on the form. Attendees must be present at the full event to receive Continuing Pharmacy Education credit, which will be awarded as follows:
Course 1 Title: Foundations of Quality Risk Management
PDA #529 | ACPE #0116-0000-17-014-L04-P | 0.6 CEUs
Type of Activity: Knowledge
Continuing Education for Professional Engineers
New Jersey: PDA is an approved provider by the New Jersey State Board of Professional Engineers and Land Surveyors to offer courses to New Jersey Professional Engineers for Continuing Professional Competency (CPC) credit. Following the full participation in this course, participants will receive a Certificate of Accomplishment specifying the number of CPC credits that may be awarded. This certificate can be submitted as verification of completion to the Board for license renewal. The credit value of this course is 6 CPC credits.
North Carolina: PDA is recognized by the North Carolina Board of Examiners for Engineers and Surveyors as an Approved Sponsor of Continuing Professional Competency (CPC) activities for Professional Engineers licensed by North Carolina. To receive a Certificate of Accomplishment specifying the number of Professional Development Hours (PDHs) that may be awarded, course participants must request the North Carolina Board of Examiners evaluation form from PDA staff. This form must be completed onsite at the conclusion of the course and returned to PDA staff. The credit value of this course is 6 PDHs.
Course 2 Title: Practical Application of Quality Risk Assessment Tools
PDA #531 | ACPE #0116-0000-17-016-L04-P |1.8 CEUs
Type of Activity: Application
Continuing Education for Professional Engineers
New Jersey: PDA is an approved provider by the New Jersey State Board of Professional Engineers and Land Surveyors to offer courses to New Jersey Professional Engineers for Continuing Professional Competency (CPC) credit. Following the full participation in this course, participants will receive a Certificate of Accomplishment specifying the number of CPC credits that may be awarded. This certificate can be submitted as verification of completion to the Board for license renewal. The credit value of this course is 18 CPC credits.
North Carolina: PDA is recognized by the North Carolina Board of Examiners for Engineers and Surveyors as an Approved Sponsor of Continuing Professional Competency (CPC) activities for Professional Engineers licensed by North Carolina. To receive a Certificate of Accomplishment specifying the number of Professional Development Hours (PDHs) that may be awarded, course participants must request the North Carolina Board of Examiners evaluation form from PDA staff. This form must be completed onsite at the conclusion of the course and returned to PDA staff. The credit value of this course is 18 PDHs.
Become a Sponsor
Interested in becoming a sponsor? Learn about opportunities and benefits.
Request InformationBecome an Exhibitor
Interested in becoming an exhibitor? Learn about opportunities and benefits.
Request InformationPLEASE READ PDA is not affiliated or contracted with any outside hotel contracting company. If someone other than PDA or the PDA chosen hotel contacts you suggesting that they represent any PDA event, they do not. It is PDA's recommendation that you book your hotel directly through the official PDA chosen hotel that is listed on our web site.
PDA Training and Research Institute
4350 East West Highway, Suite 150Bethesda, MD , United States
Course 1 Faculty
Lori Richter, Senior Consultant, Valsource, LLC
Lori Richter is a Senior Consultant at ValSource. She holds a Microbiology degree and over 18 years of experience working in the Pharmaceutical industry. Her areas of expertise include Quality Risk Management, Quality Systems, business continuity management, biotechnology manufacturing processes, and business process development. Her most recent role included developing an Integrated Risk Management program focused on strategic risk and business continuity management. Prior to that she held a global team role, developing and deploying a Quality Risk Management (QRM) program across the Roche Pharmaceutical Division, including developing tools, templates, and training materials, and integrating QRM into Quality Systems. She is currently a team member of the Parenteral Drug Association (PDA) Task Force, “Quality Risk Management for the Design, Qualification, and Operation of Manufacturing Systems”, authoring TR 54-5.
Amanda B. McFarland, Senior Consultant, Valsource, LLC
Amanda Bishop McFarland, M.S. is a Quality Risk Management and Microbiology Consultant with Valsource, LLC with over 15 years industry experience. She specializes in the creation and implementation of Risk Management programs and in developing risk-based strategies for use in Microbiology. She has a Bachelors of Science (Entomology) and a Masters of Science in Mycology both from the University of Florida. Amanda is an active member of the Parenteral Drug Association (PDA); a faculty member of the PDA’s Quality Risk Management training series and the Quality Risk Management Interest Group co-lead.
Course 2 Faculty
Ghada Haddad, Director, Global Quality Risk Management CoE, Quality Assurance and External Affairs, Merck and Company
Ghada Haddad is currently a Director at Merck & Company, leading the Global Quality Risk Management (QRM) Center of Excellence. She holds a chemistry degree and an MBA with over 18 years of experience, working in the Biotech and Pharmaceutical industries starting with Hewlett- Packard, Agilent Technologies, Genentech, Roche and now Merck in the areas of Qualification and Validation, QRM, Quality Systems and Regulatory, including research, process development, auditing, regulatory agency inspection, change control. Ghada is a PDA Board of Director member as well as a member of the Science Advisory Board. She was the task force leader of the Paradigm Change in Manufacturing (PCMO) initiative for TR54-2, QRM in Packaging and Labeling, TR54-5, Quality Risk Management for the Design, Qualification, and Operation of Manufacturing Systems, co-chair of the Aging Facility Points to Consider, a member of TR54-3, QRM in the Manufacturing of Pharmaceutical Drug Products, and a contributor to TR54, Implementation of Quality Risk Management for Pharmaceutical and Biotechnology Manufacturing Operations. Ghada is also a Faculty member for PDA’s Training and Research Institute and a frequent speaker at PDA conferences as well as a member of the Annual PDA planning committee for the past 3 years.
Scott Rudge, COO and Chairman, RMC Pharmaceutical Solutions, Inc
Since co-founding RMC Pharmaceutical Solutions in May 2004, Scott has been involved in a wide variety of projects for small and large biotech/pharmaceutical companies. He has overseen and/or performed assay, equipment, sterilization, cleaning and process validation, formulation development, due diligence for a multimillion dollar investment, construction of a new GMP facility for tissue processing, and tech transfer for a major late stage biotechnology product. In his last position, Scott served as the Vice President of Operations at FeRx Incorporated, overseeing manufacturing, process and product development, analytical development, formulation, facility design, construction and operation, and intellectual property.