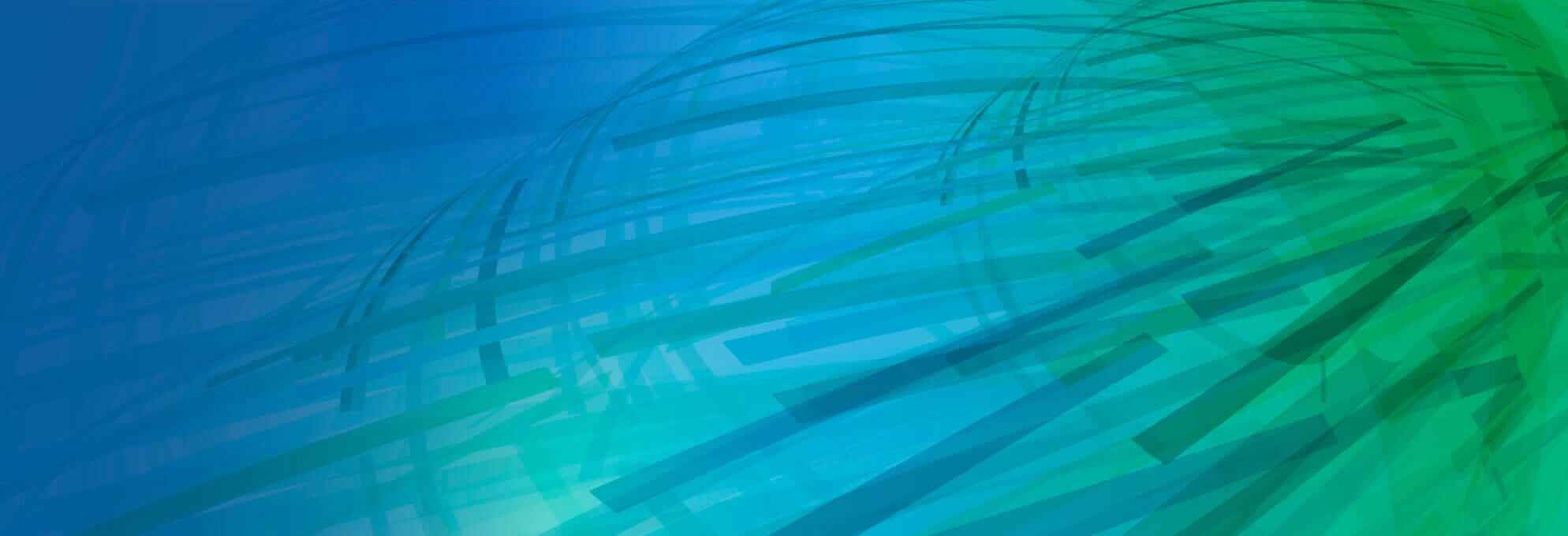
Practical Guide for Root Cause Investigations - Methodology & Tool Kit
Registration Options
Individual Registration
Group Registration
This engaging two-day workshop teaches a step by step, proven process ideal for researching any change/decline in the performance of a product or work process/system, whether it be physical or virtual. It is appropriate for individuals new to this discipline, as well as those who are seasoned veterans looking to improve/refresh their skills, regardless of industry or function within the organization. Simply put, this is one of the most practical and applicable trainings available!
On day one, the participants are introduced to the seven step methodology. A Roadmap is provided to guide the participants through the steps and suggest appropriate tools to ensure the right questions are being asked, the right data is being collected, and the right documentation is being made. After each step is presented leveraging an instructor case study, the participants immediately apply the learning on their own case study (which is based upon a real life investigation). On day two, several hours are devoted to strengthening the participants’ skills leveraging the methodology through practice on another, more complex, real life case study. As the participants work on this case study they will compare their work with that of the investigation conducted by the real team.
Participants will be emailed a set of electronic templates. These templates, plus the Roadmap, guide the investigator through the methodology and provide the basis for documentation.
Who should attend?
Alumni of this program typically (though not exclusively) have a background in:
- Quality
- Risk management
- Regulatory affairs
- Compliance
- Manufacturing
- Product development
- CAPA
- Supply chain & purchasing
- Production
- Engineering
- Project management
- R&D
- Fraud management and more
Learning Objectives
Upon completion of the workshop, participants will able to immediately, effectively, and efficiently apply the methodology to:
- Identify the technical root cause(s), that is, the change(s) that occurred.
- Identify systemic root cause(s), that is, any underlining breakdown in the organizations broader systems that allowed the change(s) to occur.
- Implement a comprehensive corrective and/or preventive action plan to restore performance.
- Implement a control plan to minimize and/or prevent recurrence.
Contact
Program Inquiries
Exhibition/Sponsorship Inquiries
Training Course Inquiries
Registration Customer Care
More information coming soon.
ALL PRICES IN EURO (EUR), EXCLUDING VAT.
WAYS TO REGISTER: 1. Online Registration 2. [email protected]
PDA MEMBERS: Please remember to log in before registering If you come from a Governmental or Health Authority Institution or from an Academic Organization, please contact [email protected] before registering.
If you need to apply for a visa to enter the event country, PDA Europe must be informed of this fact at least 4 weeks before the start of the event.
Day 1
Instructor
Rob Weaver, President of Weaver Consulting
Founded in 2003, Weaver Consulting is a two-person enterprise comprised of Tom Weaver and Rob Weaver. They are quality and operations improvement consultants who focus their business exclusively on root cause analysis. With a combined 40+ years’ experience and a client base that expands worldwide, they have helped organizations across a multitude of highly regulated industries, including pharmaceutical, medical device, aerospace, defense, financial services, food & beverage, consumer products, automotive, telecommunications, semiconductors, and many more, successfully implement their premier root cause analysis methodology, Root Cause Investigation for CAPA. Both Tom and Rob held titles of Vice President in their respective careers before joining the firm, Tom with Baxter Healthcare and Rob with Wells Fargo & Company.
Thursday, 23 November 2017
9:00
Welcome & Introduction
- Define technical CAPA problem
- Common investigation mistakes
- Investigation Roadmap template
- Introduce 1st participant real life case study
10:00
Step 1: Define the Performance Problem
- Introduce instructor case study
- Problem statement
- Problem description
10:30
Coffee Break
11:00
Step 1: Continued
- Problem description continued
- Workshop
- Flow chart process(es) being investigated & identify key inputs
- Workshop
- Time of events
- Team charter including performance & cost savings goals
12:00
Lunch Break
13:00
Step 2: Collect Data
- Determine data needed
- Data collection tools & techniques
- Data measurement plan
- Workshop
15:00
Coffee Break
15:30
Step 3: Identify Possible Causes
- Time of changes
- Differences between Is & Is Not facts
- Workshop
- Changes associated with identified differences
- Review risk analysis
- Brainstorming techniques
- Workshop
16:30
Step 4: Test Possible Causes
- Test possible causes against facts
- Summarize testing leveraging contradiction matrix
- Historical perspective of investigations
- Workshop
17:30
Step 5: Identify Technical & Systemic Root Causes
- Verify assumptions
- Conduct studies/experiments
- Identify technical root cause(s)
18:00
End of Day 1
Friday, 24 November 2017
9:00
Step 5: Continued
- Identify systemic root causes
09:30
Step 6: Determine Corrective/Preventive Actions
- Mistake proofing techniques
- Variation reduction & optimization techniques
- Corrective/preventive actions
- Acceptance criteria
10:30
Coffee Break
11:00
Step 6: Continued
- Risk mitigation
- Control plan
- Workshop
11:45
Step 7: Verify Corrective/Preventive Actions
- Implement & measure corrective/preventive actions
- Evaluate control plan
- Determine additional preventive actions
12:00
Lunch Break
13:00
Second Participant Real Life Case Study
- Introduction
- Workshop to develop problem statement, problem description, identify possible causes
- Workshop to collect data
- Workshop to test possible causes
15:00
Coffee Break
15:30
Second Participant Real Life Case Study Continued
- Workshop to determine corrective/preventive actions including risk mitigation, control plan, acceptance criteria
16:00
Closing Remarks
- Compare/contrast this investigation methodology with traditional approach
- Shortcuts
- Simple investigations
- Difficult investigations
- Investigation report
- Return on investment
- References
16:30
End of Course
Sponsorship and Exhibit Opportunities are Available!
For more information about exhibit and sponsorship opportunities, please contact:
Nadjeschda Gomez-Stahl
Manager Exhibition & Sponsorship
Tel: +49 (0) 30 43 655 08-23
Fax: +49 (0) 30 43 655 08-66
Email
Become a Sponsor
Interested in becoming a sponsor? Learn about opportunities and benefits.
Request InformationBecome an Exhibitor
Interested in becoming an exhibitor? Learn about opportunities and benefits.
Request InformationPLEASE READ PDA is not affiliated or contracted with any outside hotel contracting company. If someone other than PDA or the PDA chosen hotel contacts you suggesting that they represent any PDA event, they do not. It is PDA's recommendation that you book your hotel directly through the official PDA chosen hotel that is listed on our web site.
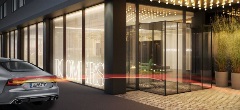
Roomers Munich
Landsberger Str. 68
80339 Munich
Germany
Tel: +49 89 12501380
Hotel Website
As the new Munich's new luxury lifestyle hotel, Roomers Munich embraces the love of special moments in life and the passion to share it. Roomers Munich is a modern contemporary lifestyle hotel with 281 rooms and suites that convinces by its exceptional interior design combined with a unique food & beverage concept and a Spa.
The Roomers Munich is a place that stands for itself creating memorable and distinctive experiences. Suites with sauna and Jacuzzi on the terrace, with a view to the Alps as well as a pool with a cinema screen leave nothing to be desired and make every visit a special occasion.
With the implementation of the award winning "Roomers Bar" concept, Roomers Munich will follow the successful footprint of the sister property in Frankfurt. The "Roomers Privée" with daily live entertainment and the "IZAKAYA" restaurant, an award-winning Japanese food restaurant from Amsterdam, are just a few examples to express the cosmopolitan lifestyle.
PDA Europe has reserved a limited number of rooms until the 18th September 2017.
Book your room for the PDA Group Rate.
Single Room € 180 per night*
Double Room € 230 per night*
- Buffet Breakfast in the restaurant
- Wireless Internet Connection (WI-FI)
- Taxes and Service will apply
How to Get There
Munich Airport – MUC
Airport Phone: +49 89 97500
Hotel direction: 25 miles SW / 40 km SW
This hotel does not provide shuttle service.
Parking
- On-site parking, fee: 4.50 EUR hourly, 25 EUR daily
- Complimentary valet parking