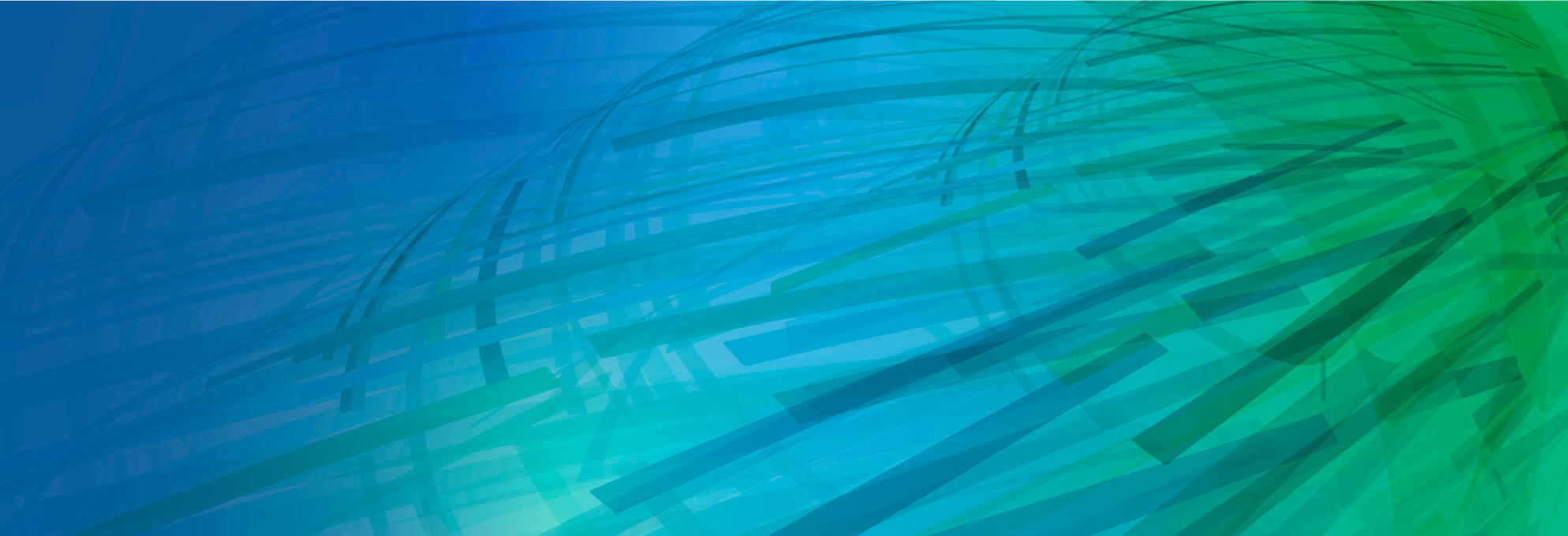
PDA EU00186 How to Handle Test Sets in Visual Inspection
Registration Options
Individual Registration
Group Registration
Program Highlights
This two-day training course will take place at Körber Pharma Inspection.
Visual inspection test sets are essential for operator qualification and validation of a visual inspection systems to be compliant with all pharma regulations, GMP requirements, and company specific quality standards.
As test sets are individually designed and developed based on the product specifications as well as the manufacturing processes, no “one-size fits all” solution is possible. Its variability regarding size, content, and purpose makes management along the life cycle of a test set even more difficult. Starting from the creation of a test set to the vision evaluation up to the correct application along the manufacturing process reflects the high level of complexity.
This training course will take place at the Körber Pharma Inspection Site in Markt Schwaben, Germany. In order to fully understand the “why do I need”, “when do I need”, “what do I need” combined with “how do I create”, “how do I apply”, and “how do I manage” a test set, experts will share their expertise based on best practices and years of experiences within the pharmaceutical industry.
- Understanding compliant VI test set design, qualification, and lifecycle management: purposes, process, and applications
- Understanding the current regulatory expectations and quality risk management of VI and particle control
- Understanding the different types of defects and their potential impact on quality
- How to develop a test kit for the visual inspection (risk analysis, what defects should be included)
- How to build up a test kit for the visual inspection (practical introduction)
- How to handle a test kit (shelf life, storage and more)
- Hands on experience on manual & automatic inspection
- The importance of a defect sample set for an AVI project
- How to handle DIP on AVI
Learning Objectives
Contact
Program Inquiries
Exhibition/Sponsorship Inquiries
Training Course Inquiries
Registration Customer Care
Standard Registration
Member Price
€ 2.090Non-Member
€ 2.090
ALL PRICES IN EURO (EUR), EXCLUDING VAT.
WAYS TO REGISTER: 1. Online Registration 2. [email protected]
PDA MEMBERS: Please remember to log in before registering If you come from a Governmental or Health Authority Institution or from an Academic Organization, please contact [email protected] before registering.
If you need to apply for a visa to enter the event country, PDA Europe must be informed of this fact at least 4 weeks before the start of the event.
Day 1
Tuesday, 13 February 2024
9:00
Welcome & Introduction of Trainers and Participants
9:15
1.1 Introduction to Test Sets for Manual Visual Inspection
- What is in principle a test set?
- Why do we need test sets?
- When should a test set be created?
- Overview of agenda of the training course
- naming the different types of test sets covered in the course
- main purpose
- timing when this type of test set will be covered during the course
- Distinction of test sets required for visual inspection from test sets required for CCI testing
9:45
1.2 Purposes of Test Sets and Background to the Test Set Qualification Process
- 100% VI and AQL
- QC testing (e.g. stability)
- Generation of supportive data for quality investigations/ Inspection support - justification of qualification process and control system
10:15
Coffee Break
10:45
1.3 Design of Test Sets
- Introduction into a flowchart that has all the necessary steps to decide on the design of the test set (the flowchart should be one of the main course deliverables)
- Why do I need a risk assessment?
- How do I perform the risk assessment?
- What must the test set look like?
- Which primary packaging do I have in the facility?
- Which particle sources do I have in the facility?
- Which product defects do I regularly see in the facility?
- Which defects must be included in my test sets?
- Relevance to quality investigations: criteria for assessment of the criticality of quality events
- Frequency of occurrence
- Typical vs Atypical
- Relevance to QC testing
- Introduction into US FDA classification
- Intrinsic
- Extrinsic
- Inherent
- Generic vs. product-specific test sets
11:45
1.4 Particles and Defects
- Overview of types of particles
- Spherical particles (balls)
- Irregular glass fragments
- Adhering particles
- Overview of other defects
- Container defects (Cracks, Scratches, Leaking)
- Stopper defects
- Cap defects or crimping defects
- Contaminations (inside outside)
- Solution defects
- How many containers must be included in the test set?
- “Defect-free” containers
- “Defective” containers
- What must my associated defect library look like?
- Types of defects
- Sizes of defects
- Major defect
- Minor defects
- Critical defects
- Which classes of defects must be included in the test set?
12:15
1.5 Introduction to Test Sets for Automated Visual Inspection
- How to handle test sets during a project?
- Test set for validation of automated visual inspection machine including AVI development test set
- Test set for daily performance check of automated visual inspection machine
- Knapp test set
12:30
Lunch Break
13:30
1.6 Tour to the Körber Vision Laboratory
Vision evaluation of a test set, step by step
- Check test set for completeness
- Visibility of defects
- Mechanical set up for test set evaluation
- How do particles behave
- Definition of camera stations and illumination for AVI
- Creation of vision configuration for AVI, based on test set
- Definition of detection rate & false eject rate of AVI
15:00
Coffee Break
15:30
1.7 Special Test Sets - What Do They Need to Look Like?
- Lyophilized products
- Difficult to inspect products
- ATMPs
- Colored glass containers
- Emulsions
- Suspensions
- Turbid liquids
- Substitute solutions versus real product
16:00
1.8 Technical Considerations on Test Sets for Difficult-to-Inspect Products
- Small volume and large volume containers
- Lyo containers
- Infusion bags
- Solutions with turbidity
- Colored solutions
- Colored containers
- Solutions with high viscosity
16:30
1.9 Challenges of Difficult to Inspect Products for Automated Visual Inspection
- Products prone to air bubbles
- Foaming products
- Highly viscous products
- Toxic products
- Lyophilized products
- Emulsions / Suspensions / Turbid liquids
17:00
Wrap up training course day 1
17:45
End of Training Course Day 1
from 18:30
Get-together
Day 2
Wednesday, 14 February 2024
09:00
What Are Your Practical Challenges with Test Sets?
09:10
2.1 Challenges from a Pharma Perspective
- Syringes/cartridges with sticky particles (due to siliconization)
- Glass defects in tubular glass containers vs molded glass containers
- Highly viscous products
- Toxic products
- Foaming products
- Air bubbles in product
09:20
2.2 Challenges from a Laboratory Perspective
- Syringes/cartridges with sticky particles (due to siliconization)
- Glass defects in tubular glass containers vs molded glass containers
- High viscose products
- Toxic products
- Foaming products
- Air bubbles in product
09:40
2.3 Challenges from the Machine Supplier’s Perspective
- Sticking/floating particles
- Glass defects in tubular glass containers vs molded glass containers
- Large volume containers
- Low fill products
- Unstable containers
- Overlapping needle shield
- Amber glass
10:00
Coffee Break
10:30
2.4 Lifecycle Management of Test Sets
- Required data and documentation:
- Certificate of manufacturing (expected characterization data)
- Qualification report
- Training certificates
- Lifecycle management:
- Storage and shelf-life
- „Disappearing“ defects
- Replacement of units
- Re-qualification
- Multi-site setup (same product different facilities) - harmonization of practices
- Phase-appropriate approaches:
- early phase vs. BLA and commercial
12:00
Lunch Break
13:00
2.5 Facility Tour at Körber Pharma Inspection Site
- Hands-on exercise 4
- Demonstration of a „simple“automated inspection machine
- Hands-on exercise 5
- Demonstration of „sophisticated” automated inspection machine
14:30
2.6 Requirements Related to Automated Visual Inspection
- Transformation of the main principles from manual visual inspection to automated visual inspection
15:30
Coffee Break
16:00
Wrap-up training course day 2
16:30
Final Wrap-up of training course
16:45
End of Training Course
Featured Trainers
-
Matthias Eisele
Material Analytischer Service
Read BioMatthias Eisele
Material Analytischer Service
Matthias Eisele studied English and chemistry at the Albert-Ludwigs-University Freiburg.
Joining M.A.S. in 2019, as a laboratory coordinator he is responsible for the seamless execution of various projects. His interest lies in the development of new methods to simulate and prepare defects and the creation of standard reference test kits for the visual inspection of parenterals.
-
Severin Gumz
Körber Pharma Inspection
Read BioSeverin Gumz
Körber Pharma Inspection
Severin Gumz is a Field Service Engineer at Körber Pharma Inspection in Germany, Markt Schwaben. He is responsible for setting up and adjusting the vision system on an inspection machine at the customer's site. Severin gained his experiences during his eight years in the vision department, one year in the academy and three years in the field service. Due to his close customer contact he is well experienced in different qualification approaches.
In his current role he trains new technicians and supports the field service engineers.
-
Marion Haberstetter
Körber Pharma Inspection
Read BioMarion Haberstetter
Körber Pharma Inspection
Marion Haberstetter is the Technical Sales Support for Inspection Applications at Körber Pharma Inspection in Germany, Markt Schwaben.
Her background in visual inspection was gathered during more than seven years of working in the vision department.
In her current role in the sales team, she is responsible for projects where the Vision System of Körber Pharma Inspection is integrated into third party machines. Also the EVE Lab-Machine is within her responsibility due to the focus on Vision.
-
Christian Kolic
Körber Pharma Inspection
Read BioChristian Kolic
Körber Pharma Inspection
Christian Kolić is a Product Manager Inspection Machines for Körber Pharma Inspection in Germany, Markt Schwaben. Christian has over 20 years’ experience in inspection of pharmaceutical products.
In his current role as product manager, he is responsible for further development and maintenance of the product portfolio and manages activities such as preparation and coordination of market and technology analyses, development and project management for the implementation of new product and service ideas.
-
Atanas Koulov
Clear Solutions Laboratories
Read BioAtanas Koulov
Clear Solutions Laboratories
Atanas is Chief Scientific Officer of Clear Solutions Laboratories, a company specializing in integrated analytical services for particle control in Biopharma. In his 15 years of industry experience (Novartis Biologics, Roche/ Genentech, Lonza and Clear Solutions Labs).
Atanas has built and led several particle characterization facilities and managed various analytical and QC groups. Prior to co-founding Clear Solutions Laboratories, Atanas established, built up and led the DP Analytical Development & QC Department at Lonza. Throughout his career Atanas has specialized in the area of particle control and characterization and has published more than 50 peer-reviewed papers on these topics.
-
Swen Maas, PhD
Material Analytischer Service
Read BioSwen Maas, PhD
Material Analytischer Service
Dr. Swen Maas studied Chemistry at the University of Freiburg and founded the Material Analytischer Service (M.A.S...) in 1997 which is located in Freiburg, Germany.
M.A.S... produces reference standard test kits for visual inspection for ampoules, BFS containers, cartridges, infusion bags, Lyo products, syringes and vials since 2002.
-
Felix Riehn, MSc
Körber Pharma Inspection
Read BioFelix Riehn, MSc
Körber Pharma Inspection
Felix Riehn holds a Master of Science degree. He joined Körber Pharma in 2014 and has worked in business development, strategic marketing and product management. After 4 years in the Swiss headquarters, he joined the world market leader 'Körber Pharma Inspection', better known as 'Seidenader'. As head of product management he is in constant exchange with pharmaceutical manufacturers and drove innovations such as 'Switch 75' or 'Deep Learning'.
Become a Sponsor
Interested in becoming a sponsor? Learn about opportunities and benefits.
Request InformationBecome an Exhibitor
Interested in becoming an exhibitor? Learn about opportunities and benefits.
Request InformationPLEASE READ PDA is not affiliated or contracted with any outside hotel contracting company. If someone other than PDA or the PDA chosen hotel contacts you suggesting that they represent any PDA event, they do not. It is PDA's recommendation that you book your hotel directly through the official PDA chosen hotel that is listed on our web site.
Körber Pharma Inspection
Lilienthalstr. 8Markt Schwaben, Germany , Germany
PDA recommends the reservation at the following hotels:
Gästehaus am Turm
Gschmeidmachergasse 2
85570 Markt Schwaben
Germany
The hotel is located 12 minutes walk from the training course venue.
Hotel Gutsgasthof Stangl
Münchener Straße 1
85646 Neufarn/Vaterstetten
Germany
The hotel is located 15 minutes car drive from the training course venue.
Bader Hotel
Heimstettener Str. 12
85599 Parsdorf bei München
Germany
The hotel is located 15 minutes car drive from the training course venue.