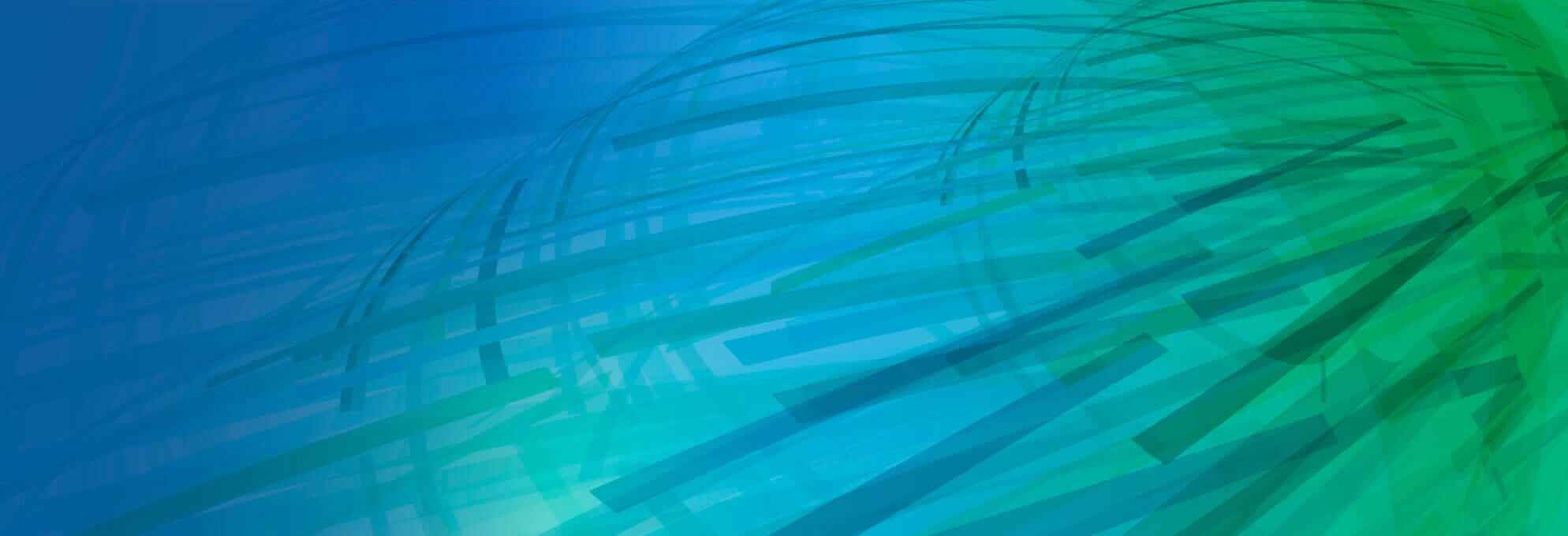
Knowledge Management Applied in Facilities & Engineering to Improve Manufacturing Reliability
Registration Options
Individual Registration
Group Registration
Time: 8:30 a.m. - 4:00 p.m.
This course will engage participants in a common goal of effecting positive change and improving equipment, facility, and utility reliability through facilities and engineering. Participants will learn to identify and anticipate equipment problems, and then apply techniques to ensure resources are provided to those equipment issues. Topics and perspectives presented will aim to provoke thought and elicit potential actions that participants can take back to their organizations, such as analyzing and presenting the cost of quality and comparing the impact of fixing the problems now, fixing them later, or fixing when it's too late. Through the lens of facilities and engineering work, this course will traverse the FDA process validation lifecycle with a punch list of many topics, some of which are: aging facilities; knowledge management; and, meaningful metrics.
Who Should Attend
Professionals in the pharmaceutical industry who have the following roles and/or responsibilities will benefit from this course:
- Engineering
- Facilities
- Maintenance
- Project Management (i.e., new build/expansion)
- Finance/Accounting
- Learning & Development
- Process Excellence
- Manufacturing
- Quality
Prerequisites
Prerequisites include expectations that participants have experience working in or working closely with Facilities & Engineering teams. Participants should have experience with some, but not all, of the following:
- Working knowledge of equipment maintenance; equipment selection including documents URS, design qualification, commissioning, etc.
- Experience with capital project requests
- Familiarity with personnel qualification and training practices
- Familiarity with departmental metrics and the data sources involved
Contact
Program Inquiries
Training Course Inquiries
Registration Customer Care
More information coming soon.
Day 1
Upon completion of this course, you will be able to:
- Introduce Cost of Quality in Facilities & Engineering (F&E) to demonstrate long term value of resource investments
- Classify Cost of Quality categories for association to F&E work at scrap, appraisal, and prevention costs
- Illustrate a Cost of Quality analysis to teach important attributes of a successful capital project proposal
- Examine current ways issues are identified in equipment/facilities/utilities and evaluate their effectiveness
- Collaborate and assemble an improved way to track and trend issues to feed Cost of Quality analyses
- Construct vision and mission statements that could be shared among F&E professionals
- Identify knowledge gaps within F&E teams and knowledge gaps outside of F&E groups
- Develop a keyword-based knowledge transfer solution that fills gaps within and outside of F&E groups
Continuing Education for Pharmacists
PDA is accredited by the Accreditation Council for Pharmacy Education (ACPE) as a provider of continuing pharmacy education. Participants may sign up to receive Continuing Pharmacy Education (CPE) credits. To do so, participants must sign in at the beginning of the program, submit the provided evaluation forms and mail the CPE credit request to the address stated on the form. Attendees must be present at the full event to receive Continuing Pharmacy Education credit, which will be awarded as follows:
PDA #513 | ACPE #0116-0000-16-005-L04-P | 1.2 CEUs
Type of Activity: Application
Continuing Education for Professional Engineers
New Jersey
PDA is an approved provider by the New Jersey State Board of Professional Engineers and Land Surveyors to offer courses to New Jersey Professional Engineers for Continuing Professional Competency (CPC) credit. Following the full participation in this course, participants will receive a Certificate of Accomplishment specifying the number of CPC credits that may be awarded. This certificate can be submitted as verification of completion to the Board for license renewal.
The credit value of this course is 12 CPC credits.
North Carolina
PDA is recognized by the North Carolina Board of Examiners for Engineers and Surveyors as an Approved Sponsor of Continuing Professional Competency (CPC) activities for Professional Engineers licensed by North Carolina. To receive a Certificate of Accomplishment specifying the number of Professional Development Hours (PDHs) that may be awarded, course participants must request the North Carolina Board of Examiners evaluation form from PDA staff. This form must be completed onsite at the conclusion of the course and returned to PDA staff.
The credit value of this course is 12 PDHs.
Become a Sponsor
Interested in becoming a sponsor? Learn about opportunities and benefits.
Request InformationBecome an Exhibitor
Interested in becoming an exhibitor? Learn about opportunities and benefits.
Request InformationPLEASE READ PDA is not affiliated or contracted with any outside hotel contracting company. If someone other than PDA or the PDA chosen hotel contacts you suggesting that they represent any PDA event, they do not. It is PDA's recommendation that you book your hotel directly through the official PDA chosen hotel that is listed on our web site.
Anaheim Marriott
700 West Convention WayAnaheim, CA ,
Chris Hanff has over 16 years’ experience in biopharmaceutical operations, quality systems, and has worked on a number of projects ranging from suite start-up and design-construction / commercialization efforts to pharmaceutical manufacturing management. He has extensive experience in essential quality management systems oversight, design, and remediation, including under FDA sanctioned consent decree.
Chris consults for the pharmaceutical industry related to quality risk management, quality systems development and deployment, lean manufacturing, value stream mapping, metrics development, statistical analyses, compliance, TrackWise, DocCompliance and similar enterprise software solutions, aseptic processing, and manufacture. He has a wide range of product experience including biotechnology, sterile product, injectables, lyophilization, medical device, and active pharmaceutical ingredients (API).
Chris has significant depth and breadth of experience as an architect of Quality Systems including: Management Review; Quality Risk Management (QRM); CAPA; Investigations; Complaints; Annual Product Review; Metrics & Trending; TrackWise EQMS; FDA mandated Consent Decree Remediation; Cost of Quality.