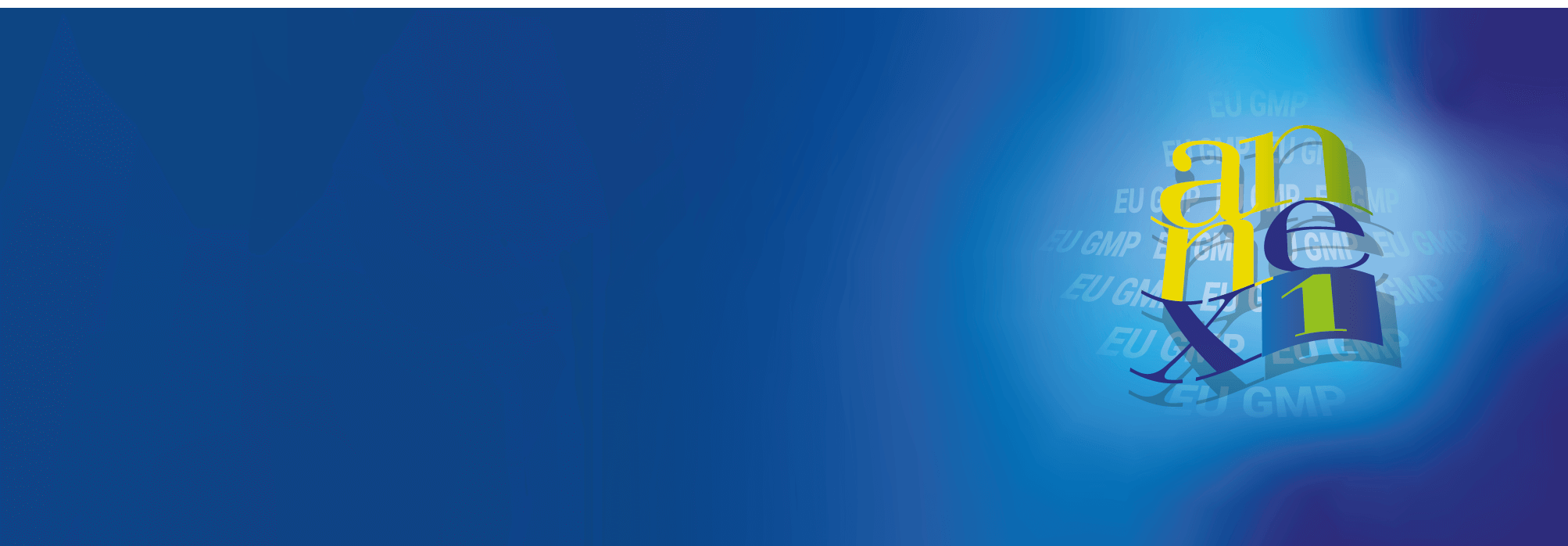
2023 PDA Annex 1 Workshop (Charlotte)
Registration Options
Individual Registration
Group Registration
Program Highlights
Benefit from six small, implementation-focused group discussions, our attendees’ favorite feature of this workshop!
Coming from Raleigh? We will be offering buses that will travel between Raleigh and Charlotte for $25 per trip. See the bus schedule for more details.
PDA is delighted to announce we will be hosting two workshops to educate and help the industry with the August 2023 implementation of the new EU GMP Annex 1 revision. PDA has and continues to be committed to developing scientifically sound, practical, technical information, and training programs to advance science and regulation for our members and the industry.
The intent of the workshops is to address the challenges and implications that have arisen with the implementation of the new EU GMP Annex 1. These workshops, scheduled for November and December, will focus on examining specific sections with critical changes and facilitating interactive sessions to provide attendees with a clear understanding of how to navigate and successfully meet the requirements of the revised EU GMP Annex 1. PDA has developed a standardized approach for workshop topics, ensuring that the information delivered to the industry remains consistent and relevant to the current regulatory landscape.
The workshops will be face-to-face, two days in length, and conducted globally (U.S. and EU). They will provide an opportunity for attendees to hear from industry experts and regulators, and open discussions with their peers' challenges and best practices.
SUBJECT MATTER EXPERTS
- Frederic Ayers, ValSource, Inc. (Co-Chair)
- Tracy Moore, TM Pharma Group Ltd. (Co-Chair)
- Richard Denk, SKAN AG
- Chris Knutsen, Bristol-Myers Squibb
- Amanda McFarland, ValSource, Inc.
- Christopher Murdock, Bristol-Myers Squibb
- Don Singer, Ecolab Life Sciences
- Kim Sobien, ValSource, Inc.
- Oliver Stauffer, Packaging Technologies & Inspection LLC
At the completion of this workshop, participants will be able to:
- Gain awareness of the requirements and changes in Annex 1 and move towards compliance with the new changes in the revision
- Develop strategies for implementation and verification of the Annex 1 requirements, respectively, for their organizations
Contact
Program Inquiries
Exhibition/Sponsorship Inquiries
Training Course Inquiries
Registration Customer Care
Standard Registration
Member Price
$2,495GovernmentMember Only
$895
Health AuthorityMember Only
$895
Early Career ProfessionalMember Only
$1,395
StudentMember Only
$595
AcademicMember Only
$895
Non-Member
$2,895
GROUP REGISTRATION DISCOUNT: Register 3 people from the same organization as a group (at the same time) for the event and receive the 4th registration free. Other discounts cannot be applied.
GENERAL TERMS AND CONDITIONS: PDA will send you a confirmation letter within one week of payment being received. You must have this confirmation letter to be considered enrolled in a PDA event. If you have submitted a purchase order or requested an invoice, please be advised that a credit card guarantee is needed. PDA reserves the right to modify the material or speakers/trainers without notice or to cancel an event. If an event is cancelled, registrants will be notified by PDA immediately and will receive a credit (registration fee paid). PDA will not be responsible for any costs incurred by registrants due to cancellation. Please note that the attendee list is shared with attendees, trainers, and exhibitors and may be used to follow up on specific areas of interest after the event. Video, photo, and audio recordings are prohibited at all PDA events.
CANCELLATION: If a cancellation request is received 30 days before the event, a credit (registration fee paid minus a 200.00 USD/EUR processing fee) will be given. No credits will be given for cancellation requests received less than 30 days before the event. Cancellation requests must be emailed to [email protected].
Day 1
MONDAY, 04 DECEMBER
07:00 – 18:00 | Registration Open
07:00 – 08:00 | Continental Breakfast
08:00 – 09:30 | P1: Overview of and Revision Process for Annex 1 The journey to the published Annex 1 has been a long and winding road that included multiple sets of industry reviews, comments, and revisions. The approved version of the Annex presents a diverse, international perspective on regulatory expectations, recommendations, and requirements for modern sterile drug and biologic product manufacturing. The published Annex 1 contains a significant amount of new content along with more detail for existing content. It places a heightened emphasis on the use of Quality Risk Management through risk assessment and contamination control through appropriate design. This session will provide insights from regulatory authorities involved in the Annex 1 development and review process of the revision, with a focus on the evolution, planning, and implementation of these changes. |
08:00 | Welcome Remarks from Workshop Co-Chairs 08:20 | Regulatory Perspective 08:45 | Insights from a Former Regulator 09:05 | Q&A with Additional Panelists |
09:30 – 10:00 | Networking Break in the Exhibit Area
10:00 – 11:00 | P2: Scope, Principles and Pharmaceutical Quality Systems This session opens our in-depth look at the content of the draft Annex 1. The Scope, Principles, and Pharmaceutical Quality System sections introduce the vision of the Annex 1 changes that track through all other sections. Talks will highlight Annex 1 focal points including contamination control strategy, quality risk management, and quality culture, including a discussion on the importance of human factors: knowledge, attitude, and experience. This session will also address the expanded scope of Annex 1 to include some non-steriles. |
10:00 | Using Quality Risk Management to Enable the Contamination Control Strategy 10:25 | Considerations of Annex 1 for Advanced Therapy Medicinal Products and Low Bioburden Products 10:55 – 11:15 | Q&A |
11:15 – 11:45 | Breakout Session 1 Attendees will discuss the implementation challenges, and what can be done to meet those challenges, associated with the topics presented in P1: Overview of and Revision Process for Annex 1 and P2: Scope, Principles, and Pharmaceutical Quality Systems. |
11:45 – 13:00 | Lunch
13:00 – 14:00 | P3: Premises and Barrier Systems Aseptic manufacturing facilities come in a variety of shapes and sizes, from traditional aseptic through restricted access barrier systems (RABS) and into Isolators. This session will take a look at some of the key design and operational aspects that have been impacted by the revised Annex 1. |
13:00 | Cleanroom Design: Classification, Qualification, Air Visualization 13:20 | Cleanroom Operation: Disinfection, Transfer of Materials, Monitoring 13:40 | Barrier Technologies: RABS and Isolators, Glove Integrity, Robotics, Decontamination 14:00 – 14:15 | Q&A |
14:15 – 14:45 | Breakout Session 2 Attendees will discuss the implementation challenges, and what can be done to meet those challenges, associated with the topics presented in P3: Premises and Barrier Systems. |
14:45 – 15:15 | Networking Break in the Exhibit Area
15:15 – 16:15 | P4: Equipment, Technology, and Utilities This session will discuss the impact of the Annex 1 revision on aseptic manufacturing facilities, specifically focusing on equipment design, indirect product contact parts, such as stopper bowls, and critical utilities, such as water systems. |
15:15 | Material Transfer 15:35 | Decontamination and Sterilization of Direct and Indirect Product Contact Surfaces 15:55 | Aseptic Process Simulations 16:15 – 16:30 | Q&A |
16:30 – 17:00 | Breakout Session 3 Attendees will discuss the implementation challenges, and what can be done to meet those challenges, associated with the topics presented in P4: Equipment, Technology, and Utilities. |
17:00 – 17:30 | Day 1 Q&A and Panel Discussion Panelists: |
17:30 – 18:30 | Networking Reception in Exhibit Area
Day 2
TUESDAY, 05 DECEMBER
07:00 – 16:00 | Registration Open
07:00 – 08:00 | Continental Breakfast
08:00 – 09:00 | P5: Personnel Training, Qualification, Gowning, and Monitoring/Assessment Training and qualifying operators are of critical importance to ensuring proper aseptic technique and cleanroom behavior. Routine monitoring of personnel ensures that the qualified personnel are following the established procedures and that they can meet the strict gowning cleanliness requirements during normal operations. Trending and analysis of gloves and gown environmental monitoring (EM) data can provide critical feedback on individual operator performance, potential routes of contamination, specific gowning procedures, and overall training efficacy. |
08:00 | Day 1 Report Out 08:20 | Qualification and Training 08:40 | Gowning, Personnel Monitoring, and Beyond 09:00 – 09:15 | Q&A |
09:15 – 09:45 | Breakout Session 4 Attendees will discuss the implementation challenges, and what can be done to meet those challenges, associated with the topics presented in P5: Personnel Training, Qualification, Gowning, and Monitoring/Assessment. |
09:45 – 10:15 | Networking Break in the Exhibit Area
10:15 – 11:00 | P6: Production Technologies, Part 1 This session will focus on the Annex 1 requirements for aseptic processing and filtration of sterile products. The aseptic processing discussion will address the types of operations and grades needed for aseptic preparation and processing operations. The filtration and sterilization presentation will provide insight into the different types of sterilization and the parameters needed to demonstrate success. |
10:15 – 10:35 | Aseptic Processing 10:35 – 11:00 | Filtration and Pre-Use Post Sterilization Integrity Testing 11:00 – 11:15 | Q&A |
11:15 – 11:45 | Breakout Session 5 Attendees will discuss the implementation challenges, and what can be done to meet those challenges, associated with the topics presented in P6: Production Technologies, Part 1 (Aseptic Processing and Filtration and Pre-Use Post Sterilization Integrity Testing). |
11:45 – 13:00 | Lunch
13:00 – 13:40 | P7: Production Technologies, Part 2 This session will introduce some of the more intriguing topics covered and expanded in the revised Annex 1, which were selected based on input from the sterile product manufacturing community, as noted during prior meetings and discussions. |
13:00 | Container Closure Integrity Testing and Finishing 13:20 | Production and Specific Technologies (Blow-Fill-Seal, Lyophilization, Single Use System, and Terminal Sterilization) 13:40 – 14:00 | Q&A |
14:00 – 14:30 | Breakout Session 6 Attendees will discuss the implementation challenges, and what can be done to meet those challenges, associated with the topics presented in P7: Production Technologies, Part 2 (Container Closure Integrity Testing and Finishing and Production and Specific Technologies (Blow-Fill-Seal, Lyophilization, Single Use System, and Terminal Sterilization). |
14:30 – 15:00 | Networking Break in the Exhibit Area
15:00 – 16:30 | P8: Aseptic Process Simulation and Environmental Monitoring APS has been identified as one of the key aspects of aseptic process control and monitoring. This session will review the related changes and begin discussing the interpretation and implementation of these recommendations and requirements. The presentations will focus on the Annex 1 requirements for APS (media fills) and environmental and process monitoring, including the new requirements and considerations for qualifying and operating a clean area and the extensive new requirements needed to successfully validate an aseptic process. |
15:00 | Environmental and Process Monitoring 15:20 | Contamination Control Strategy Development 15:40 – 16:20 | Q&A, and Panel Discussion with Additional Panelists 16:20 – 16:25 | Day 2 Report Out 16:25 | Closing Remarks from Workshop Co-Chairs |
Become a Sponsor
Interested in becoming a sponsor? Learn about opportunities and benefits.
Request InformationBecome an Exhibitor
Interested in becoming an exhibitor? Learn about opportunities and benefits.
Request InformationPLEASE READ PDA is not affiliated or contracted with any outside hotel contracting company. If someone other than PDA or the PDA chosen hotel contacts you suggesting that they represent any PDA event, they do not. It is PDA's recommendation that you book your hotel directly through the official PDA chosen hotel that is listed on our web site.
Harris Conference Center
3216 CPCC Harris Campus Dr.Charlotte, NC ,
The Workshop will take place at the Harris Conference Center (3216 CPCC Harris Campus Dr.).
PDA does not have a block of hotel room, but recommends these nearby hotels:
The Hyatt Place Charlotte Airport/Billy Graham Parkway is 2.7 miles from the Harris Conference Center
The Sheraton Charlotte Airport Hotel is 2.0 miles from the Harris Conference Center
- Average Taxi Price - $17.00 USD
- Average Uber Price- $8.00 USD