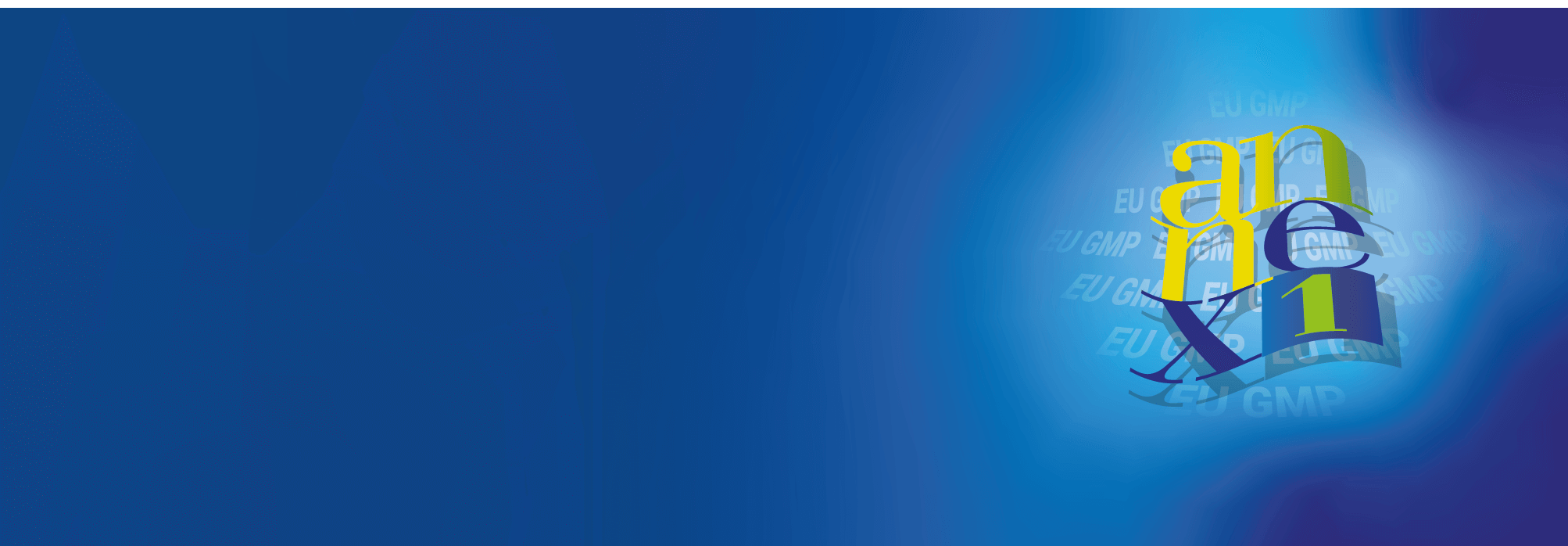
2022 PDA Annex 1 Workshop (Palm Springs)
Registration Options
Individual Registration
Group Registration
Program Highlights
The new Annex 1 revision was recently released! At this workshop, experts on the revision will answer your most pressing questions and provide solutions for implementation challenges at your organization.
This is the final workshop in a series that PDA has hosted in 2022 to educate and help the industry implement the new Annex 1 revision. PDA has and continues to be committed to developing scientifically sound, practical, technical information, and training programs to advance science and regulation for our members and the industry as a whole.
The intent of the workshops is to highlight specific sections with critical changes and include interactive sessions to provide attendees with clear understanding of and means to implement the requirements of the new Annex 1, in order to address the regulatory expectations. PDA has developed a standardized approach for workshop topics to ensure consistency in the information delivered to the industry.
This workshop will provide an opportunity for attendees to hear from industry experts and regulators, and open discussions with their peers’ challenges and best practices.
At the completion of this workshop, participants will be able to:
- Gain awareness of the requirements and changes in Annex 1 and move towards compliance with the proposed changes in the revision
- Develop strategies for implementation and verification of the Annex 1 requirements, respectively, for their organizations
Event Location
Contact
Program Inquiries
Exhibition/Sponsorship Inquiries
Training Course Inquiries
Registration Customer Care
Standard Registration
Member Price
$2,195Early Career ProfessionalMember Only
$1,095
Non-Member
$2,495
GROUP REGISTRATION DISCOUNT: Register 3 people from the same organization as a group (at the same time) for the event and receive the 4th registration free. Other discounts cannot be applied.
GENERAL TERMS AND CONDITIONS: PDA will send you a confirmation letter within one week of payment being received. You must have this confirmation letter to be considered enrolled in a PDA event. If you have submitted a purchase order or requested an invoice, please be advised that a credit card guarantee is needed. PDA reserves the right to modify the material or speakers/trainers without notice or to cancel an event. If an event is cancelled, registrants will be notified by PDA immediately and will receive a credit (registration fee paid). PDA will not be responsible for any costs incurred by registrants due to cancellation. Please note that the attendee list is shared with attendees, trainers, and exhibitors and may be used to follow up on specific areas of interest after the event. Video, photo, and audio recordings are prohibited at all PDA events.
CANCELLATION: If a cancellation request is received 30 days before the event, a credit (registration fee paid minus a 200.00 USD/EUR processing fee) will be given. No credits will be given for cancellation requests received less than 30 days before the event. Cancellation requests must be emailed to [email protected].
Day 1
THURSDAY, 20 OCTOBER
08:00 – 09:30 | P1: Overview of and Revision Process for Annex 1 Over the past four years, the revised Annex 1 has gone through multiple sets of industry review, comment, and revision. The current version presents a diverse, international perspective on regulatory expectations, recommendations, and requirements for modern sterile drug and biologic product manufacturing. The revised Annex 1 contains a significant amount of new and more detailed content on many topics. It places a heightened emphasis on the use of risk-based assessment and approaches to design and evaluate manufacturing contamination control. This session will provide insights from regulatory authorities involved in the Annex 1 development and review process of the revision, with a focus on the evolution, planning, and implementation of these changes. |
08:00 | Welcome Remarks from Workshop Co-Chair 08:20 | Regulatory Perspective 08:40 | Insights from a Former Regulator 09:00 | Q&A with Additional Panelist |
09:30 – 10:00 | Break in Exhibit Area
10:00 – 11:15 | P2: Scope, Principles and Pharmaceutical Quality Systems This session opens our in-depth look at the content of the draft Annex 1. The Scope, Principles, and Pharmaceutical Quality System sections introduce the vision of the Annex 1 changes that track through all other sections. Talks will highlight Annex 1 focal points including contamination control strategy, quality risk management, and quality culture, including a discussion on the importance of human factors: knowledge, attitude, and experience. This session will also address the expanded scope of Annex 1 to include some non-steriles. |
10:00 | Using Quality Risk Management to Enable the Contamination Control Strategy 10:20 | Aseptic Process Simulations 10:40 | Considerations of Annex 1 for Advanced Therapy Medicinal Products and Low Bioburden Products 11:00 | Q&A |
11:15 – 12:00 | Breakout Session 1 Attendees will discuss the implementation challenges, and what can be done to meet those challenges, associated with the topics presented in P1: Overview of and Revision Process for Annex 1 and P2: Scope, Principles, and Pharmaceutical Quality Systems. |
12:00 – 13:00 | Lunch
13:00 – 14:15 | P3: Premises and Barrier Systems Aseptic manufacturing facilities come in a variety of shapes and sizes, from traditional aseptic through restricted access barrier systems (RABS) and into Isolators. This session will take a look at some of the key design and operational aspects that have been impacted by the revised Annex 1. |
13:00 | Cleanroom Design: Classification, Qualification, Air Visualization 13:20 | Cleanroom Operation: Disinfection, Transfer of Materials, Monitoring 13:40 | Barrier Technologies: RABS and Isolators, Glove Integrity, Robotics, Decontamination 14:00 | Q&A with Additional Panelist |
14:15 – 15:00 | Breakout Session 2 Attendees will discuss the implementation challenges, and what can be done to meet those challenges, associated with the topics presented in P3: Premises and Barrier Systems. |
15:00 – 15:30 | Break in Exhibit Area
15:30 – 16:30 | P4: Equipment, Technology, and Utilities This session will discuss the impact of the Annex 1 revision on aseptic manufacturing facilities, specifically focusing on equipment design, indirect product contact parts, such as stopper bowls, and critical utilities, such as water systems. |
15:30 | Water Systems and Other Critical Utilities 15:50 | Decontamination and Sterilization of Direct and Indirect Product Contact Surfaces 16:10 | Q&A |
16:30 – 17:15 | Breakout Session 3 Attendees will discuss the implementation challenges, and what can be done to meet those challenges, associated with the topics presented in P4: Equipment, Technology, and Utilities. |
17:15 – 18:30 | Networking Reception
Day 2
FRIDAY, 21 OCTOBER
08:00 – 09:15 | P5: Personnel Training, Qualification, Gowning, and Monitoring/Assessment Training and qualifying operators are of critical importance to ensuring proper aseptic technique and cleanroom behavior. Routine monitoring of personnel ensures that the qualified personnel are following the established procedures and that they can meet the strict gowning cleanliness requirements during normal operations. Trending and analysis of gloves and gown environmental monitoring (EM) data can provide critical feedback on individual operator performance, potential routes of contamination, specific gowning procedures, and overall training efficacy. |
08:00 | Day 1 Report Out 08:20 | Qualification and Training 08:40 | Gowning, Personnel Monitoring, and Beyond 09:00 | Q&A with Additional Panelist |
09:15 – 09:45 | Breakout Session 4 Attendees will discuss the implementation challenges, and what can be done to meet those challenges, associated with the topics presented in P5: Personnel Training, Qualification, Gowning, and Monitoring/Assessment. |
09:45 – 10:15 | Break in Exhibit Area
10:15 – 11:20 | P6: Production Technologies, Part 1 This session will focus on the Annex 1 requirements for aseptic processing and filtration of sterile products. The aseptic processing discussion will address the types of operations and grades needed for aseptic preparation and processing operations. The filtration and sterilization presentation will provide insight into the different types of sterilization and the parameters needed to demonstrate success. |
10:15 | Aseptic Processing 10:40 | Filtration and Pre-Use Post Sterilization Integrity Testing 11:05 | Q&A |
11:20 – 12:00 | Breakout Session 5 Attendees will discuss the implementation challenges, and what can be done to meet those challenges, associated with the topics presented in P6: Production Technologies, Part 1 (Aseptic Processing and Filtration and Pre-Use Post Sterilization Integrity Testing). |
12:00 – 13:00 | Lunch
13:00 – 13:50 | P7: Production Technologies, Part 2 This session will introduce some of the more intriguing topics covered and expanded in the revised Annex 1, which were selected based on input from the sterile product manufacturing community, as noted during prior meetings and discussions. |
13:00 | Container Closure Integrity Testing and Finishing 13:20 | Production and Specific Technologies (Blow-Fill-Seal, Lyophilization, Single Use System, and Terminal Sterilization) 13:40 | Q&A |
13:50 – 14:30 | Breakout Session 6 Attendees will discuss the implementation challenges, and what can be done to meet those challenges, associated with the topics presented in P7: Production Technologies, Part 2 (Container Closure Integrity Testing and Finishing and Production and Specific Technologies (Blow-Fill-Seal, Lyophilization, Single Use System, and Terminal Sterilization). |
14:30 – 15:00 | Break in Exhibit Area
15:00 – 16:45 | P8: Aseptic Process Simulation and Environmental Monitoring Aseptic process simulation (APS) has been identified as one of the key aspects of aseptic process control and monitoring. This session will review the related changes and begin discussing the interpretation and implementation of these recommendations and requirements. The presentations will focus on the Annex 1 requirements for APS (media fills) and environmental and process monitoring, including the new requirements and considerations for qualifying and operating a clean area and the extensive new requirements needed to successfully validate an aseptic process. |
15:00 | Environmental and Process Monitoring 15:20 | Contamination Control Strategy Development 15:40 | Day 2 Report Out 15:55 | Q&A and Final Discussion with Additioanl Panelists |
Become a Sponsor
Interested in becoming a sponsor? Learn about opportunities and benefits.
Request InformationBecome an Exhibitor
Interested in becoming an exhibitor? Learn about opportunities and benefits.
Request InformationPLEASE READ PDA is not affiliated or contracted with any outside hotel contracting company. If someone other than PDA or the PDA chosen hotel contacts you suggesting that they represent any PDA event, they do not. It is PDA's recommendation that you book your hotel directly through the official PDA chosen hotel that is listed on our web site.

Book within the PDA block and be automatically entered to win a daily treat delivered to your hotel room!
A block of rooms have been reserved for meeting participants at the Renaissance Palm Springs Hotel. The group rate is $199 for single or double occupancy. Please be aware that 1 nights deposit will be charged at booking when reserving a room at the Hilton Palm Springs. Guestroom rates are subject to State and Local taxes. Reservations must be secured by Friday, 23 September 2022. After this date, reservations can be made on a space-and-rate available basis only.
To make reservations, individuals may click on the reservation link above or call the Renaissance Palm Springs Hotel at +1 (888) 236-2427. Be sure to tell the reservationist that you are with the PDA Meeting to receive the PDA group rate.
Individual Cancellation
Please be aware that obtaining and canceling hotel reservations is the responsibility of the meeting registrant. Individuals will be responsible for payment of their own cancellation fees. The cancellation policy is 3 days in advance of arrival unless otherwise specified on your reservation information.
Savor beauty inside and out when you stay at the Renaissance Palm Springs Hotel. Set against a backdrop of swaying palm trees and the majestic San Jacinto Mountains, our Coachella Valley hotel captures the essence of desert living. Find your oasis while lounging beside one of the area's largest outdoor pools or sipping a refreshing drink in one of our private cabanas. Slip into sweet dreams in rooms and suites redesigned to pamper and please with pillowtop mattresses and spa-inspired bathrooms. Whether you desire a soothing massage or rejuvenating facial during your getaway, allow Spa Del Sol to anticipate your desires. Celebrate the area while delighting in a meal at Date, our casual restaurant where the locally grown fruit graces the menu. Rocks offers a trendy bar setting to unwind after a day of exploring the Palm Springs Aerial Tramway, Palm Springs Art Museum and boutique shops along the city's main thoroughfare. Indulge in the ultimate relaxation at Renaissance Palm Springs Hotel.